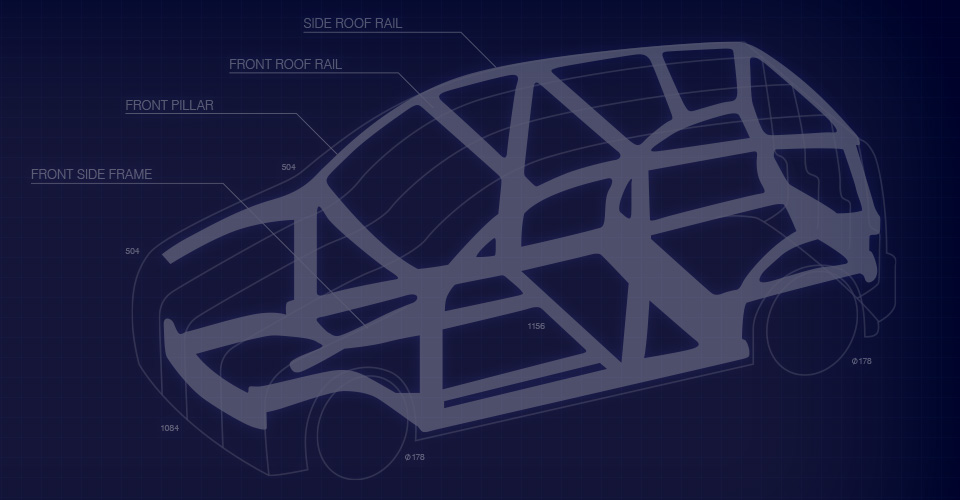
STAF created by maintaining a comprehensive customer perspective
Automobile frames that are created by pressing steel tubes with a pressing machine.
Previously, it was necessary to perform processes to remove burrs and weld joint components later.
Innovative technology to eliminate the labor and make materials lighter: STAF.
What was considered crucial in the development project---
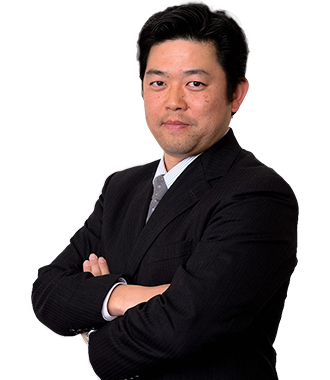
Corporate Planning Dept.
Corporate Planning Group
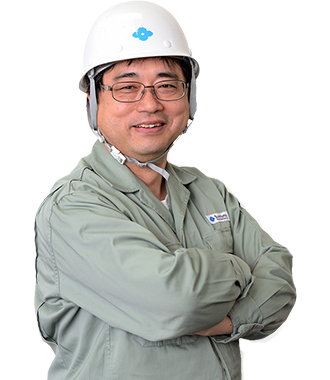
Material Engineering Dept.
Technology Reseach Center
Corporate Technology Management Group
What is in demand for automobiles
- Managing both excellent fuel efficiency and safety
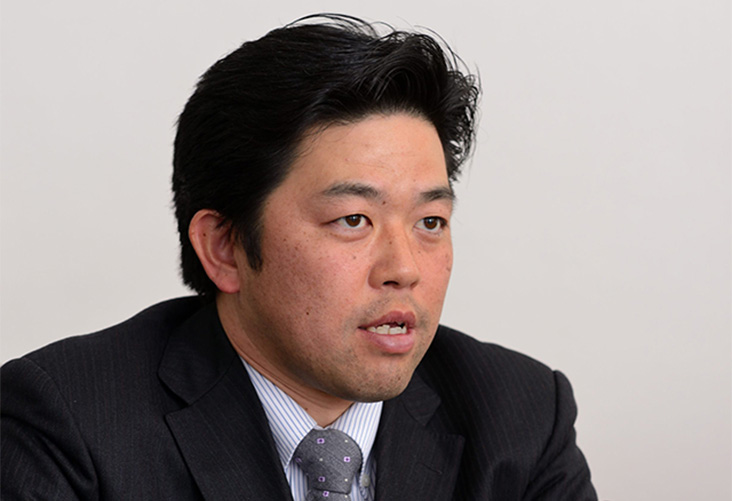
What is in demand for automobiles today is environmental performance such as better fuel efficiency and lighter weight. The lighter the body becomes, the better the fuel efficiency gets. If the materials become lighter and rigidity is lost, however, safety, which is another challenge, will be compromised. This is a dilemma that makes it difficult to kill two birds with one stone. Nevertheless, the environmental standards that are imposed on automobiles in society are becoming more stringent. For the automobile industry, there is pressing demand for the breakthrough of manufacturing methods to make lighter and safer vehicles.
One example is the steel frames that support the body. It is common to make them by the metallic mold pressing of steel sheets. Several methods have been used in the past, including sheet metal stamping and hot stamping. There were several challenges, such as difficulties in making them lighter, and complicated processes and facilities.
What made an appearance in this situation was STAF, which was developed by Sumitomo Heavy Industries. STAF stands for Steel Tube Air Forming, and it is a method of passing a strong electric current through the steel tubes, and blow molding them with high pressure air and hardening them simultaneously. This makes it possible to perform the integrated forming of the frame and the flange, which is a brim-like component that is essential for assembling a frame. In other words, there is no need to connect the flange at a later stage by welding, and therefore rigidity will be improved and the processes can be simplified. Higher rigidity in this manufacturing method means lighter weight. The ability to simplify the processes is directly related to reducing manufacturing costs.
The task of making the seeds of the technology research centers sprout and delivering them as products to the market
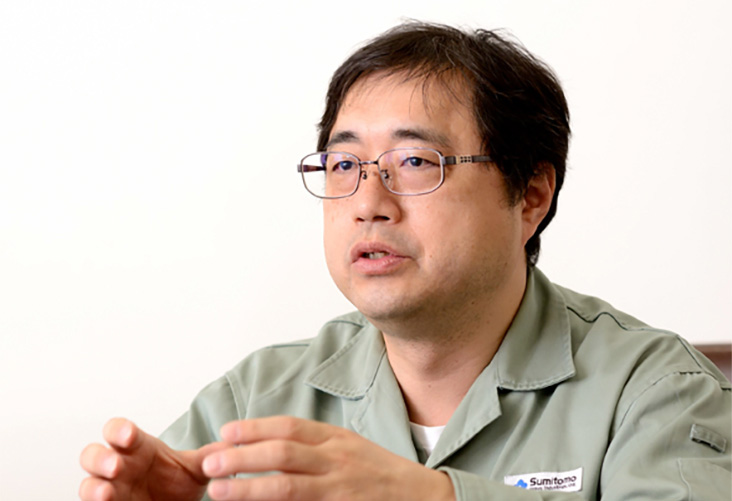
"With regard to the body frame manufacturing method, we went into the market later. However, it was a mandatory challenge to enter this field in order to stay ahead of our overseas competitors, who are trying to catch up with us in terms of the technological aspects. We commenced fundamental research in the technology research center where I worked at that time. I became acquainted with a technological venture at the Tokyo Motor Show in 2011, and I participated in the study meetings and gained knowledge of on-vehicle component technology," said Senior Engineer of Corporate Planning Group, looking back on the situation at the time.
Mr. Takashi Komatsu, a technology consultant who has experience working in the technology research center of a major automobile manufacturer, joined the study meetings. Senior Engineer of Corporate Planning Group did not miss his words at one meeting: "In order to achieve lighter weight, there is a method of forming the frame and flange all at once by feeding in high pressure air..." That was STAF. Although the idea of STAF existed, no company had developed it successfully.
It was not certain whether Sumitomo Heavy Industries could do it. However, it was worthwhile to take on the challenge. Senior Engineer of Corporate Planning Group immediately went around the related people in the company and attempted to persuade them. He wanted to achieve his own mission to make the seeds of the technology research centers sprout and deliver them as products to the market.
In 2013, the STAF process verification project was launched in the technology research center, and he asked the press design group of the Industrial Equipment Division for their support. In 2015, the project office was moved to Niihama, and repeated verification experiments were conducted. Specialized engineers were invited from design subsidiaries such as Sumimec Engineering. Despite the select few of a total of eight people, the members were excited about the engineering challenge, which nobody in the world had attempted.
"The most challenging task was to consider forming conditions including material characteristics and mold design. We conducted more than 200 tests for forming one shape. We managed to reach the point of making it technologically possible, but it was not sufficient. We needed to complete equipment that was easy for our clients, who are automobile part manufacturers, to use. In addition to technology, a marketing sense is required at the same time," said Senior Engineer of Technology Research Center, who continues to support Senior Engineer of Corporate Planning Group. What is required for people involved in research and development is to maintain a comprehensive customer perspective. This was what Senior Engineer of Corporate Planning Group always talked about repeatedly.
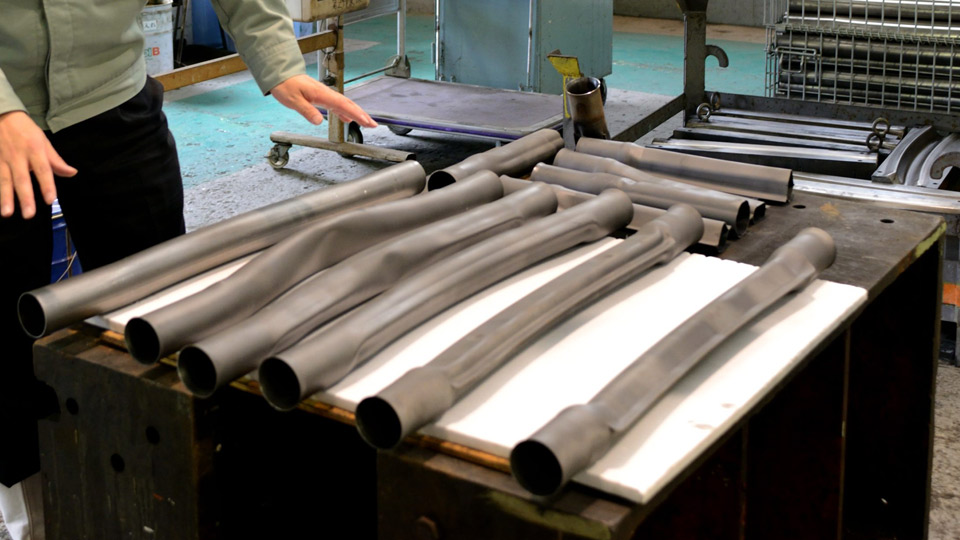
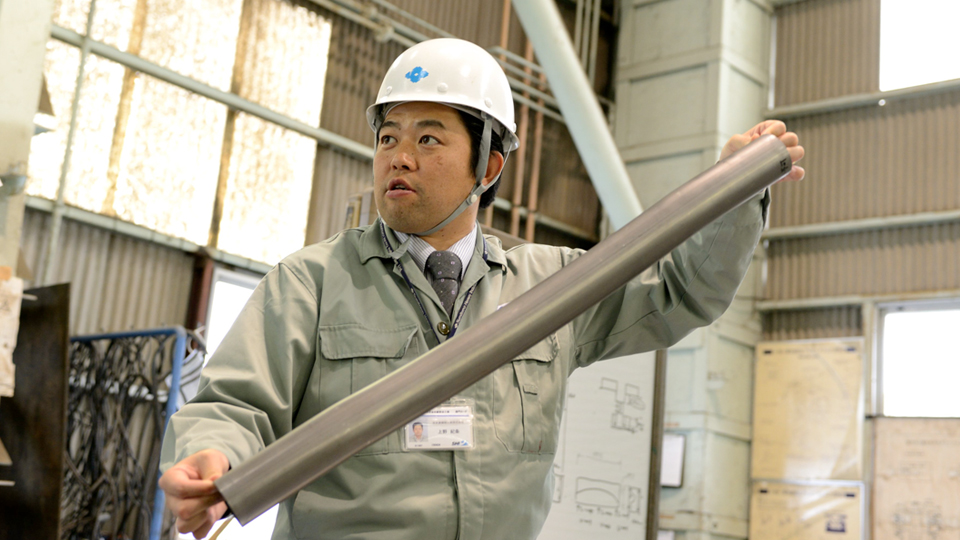

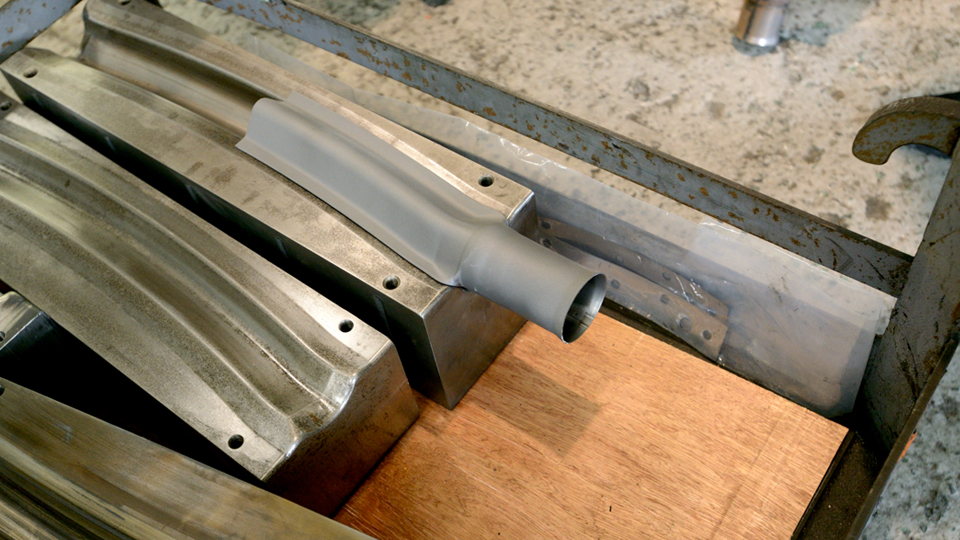
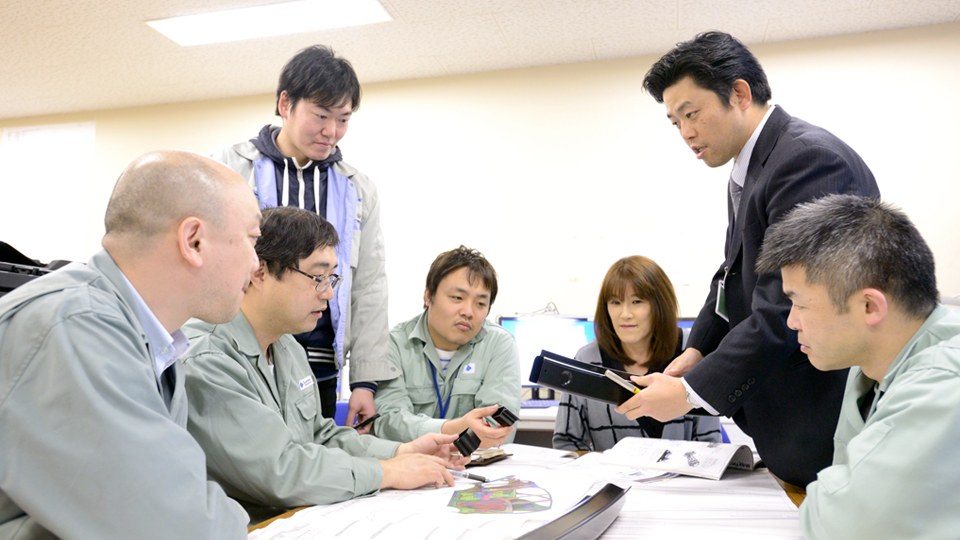
Importance of proposing contents instead of substances
As the experiment data was collected, the conditions of the computer simulations became ready. It was found to be possible to improve the withstanding load of the body frame by 30% or more than other press forming by adopting STAF. In the case of the same withstanding load, sheets can be thinner and lighter. There is no need to remove burrs or perform spot welding for flanges at a later stage.
"The present trial calculation revealed that the new technology would contribute to reducing the costs for the press process of a body frame by at least 20%, and saving the space to install the manufacturing system. We will develop the evaluation machine in FY2016, and work to propose it to automobile parts manufacturers and so on," said Senior Engineer of Corporate Planning Group proudly.
When it was announced for the first time at the Automotive Weight Reduction Expo held in January 2016 that Sumitomo Heavy Industries had been working on the development of STAF, the booth became crowded with people.
If STAF is adopted, the press process for body frames, which has been utilized for decades, will be changed dramatically. However, this does not mean that there are no challenges. The drawback of STAF is low processing applicability compared with other engineering methods. For example, there is room for the development of complicated shapes such as pipes that are bent in a longitudinal direction. Improving versatility will be a challenge for the future.
We went to the prefectural government and the Ministry of Economy, Trade and Industry many times to discuss the interpretation of the laws and ask for understanding, because large high pressure compressors, which were rare in Japan, were planned to be installed in Niihama. Finally, the day when these efforts will be rewarded is coming. Senior Engineer of Corporate Planning Group learned a lot of things through this project.
"Manufacturers and suppliers around the world are engaged in fierce competition to make automobiles lighter. They may all become our customers. To this end, it is indispensable to foresee and propose instead of waiting until we are told by customers and then taking action. That's what I learned through this project. Another key point is to propose contents, instead of substances. Customers do not only want new, inexpensive pressing machines, but also seek a system that can manufacture high quality parts in a stable manner. It is important to pursue the extent to which we can meet their expectations."
*All contents are as of the time of the interview.
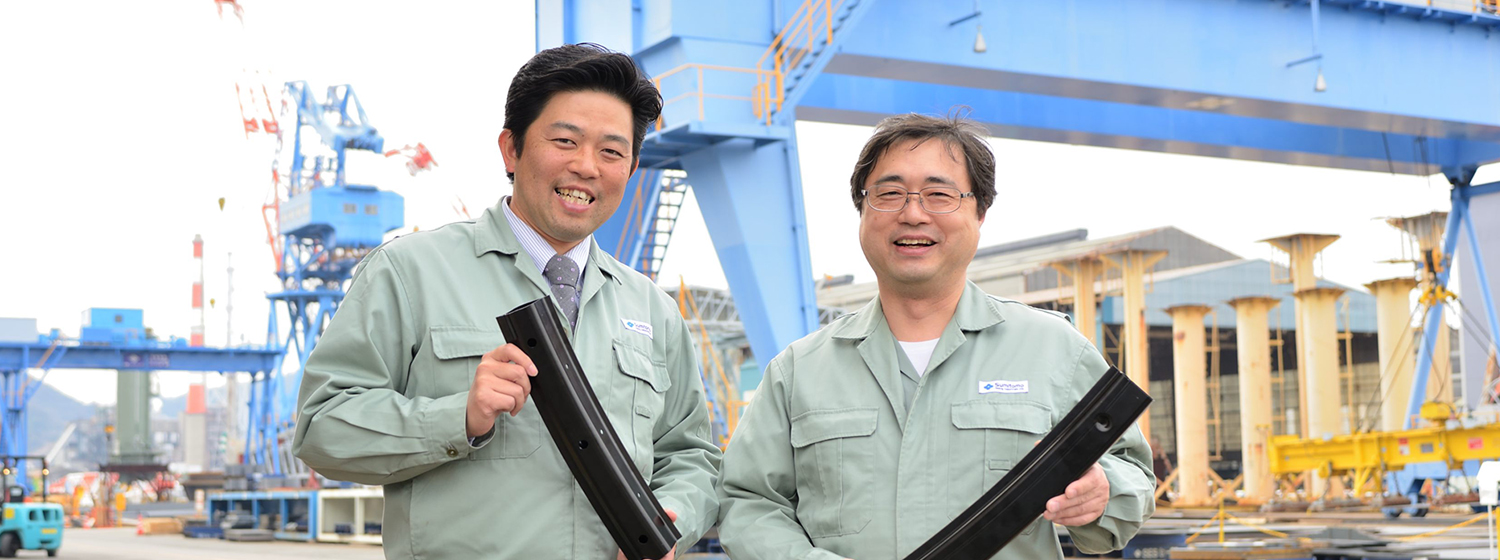
SHI Pride
- Vol.1 A Clear View of the Distant Heavens
- Vol.2 Cures without Surgery: Advanced Cancer Treatment
- Vol.3 Exploring the Mysteries of Space
- Vol.4 Dramatically Changing Quayside Cargo Handling
- Vol.5 Cyclo Drives Continue to Evolve
- Vol.6 The Steam Turbine - Protecting the Environment and Advancing Society
- Vol.7 Persistent Determination to Reduce Defects, Losses and Faults to Zero
- Vol.8 Treating Cancer through the Use of Neutrons - A Compact Accelerator Opens the Door to Widespread Use -
- Vol.9 Automated storage system with unrestricted movement, for transforming the future of the logistics industry
- Vol.10 Anaerobic Wastewater Treatment and Biogas Power Generation System using Ume Seasoning Effluent bringing Recycling-Friendly Society
- #01 Technology that has the potential to dramatically change automobile frame manufacturing STAF created by maintaining a comprehensive customer perspective
- #02 The ECY Series:A smaller Gear reducer after over 10 years of development
- #03 Cancer Therapy System "Boron Neutron Capture Therapy (BNCT system)"
- #04 Supporting Development with Innovative Simulation Technology: RMD and MBM