Cast Iron & Steel Rolls for Hot Rolling
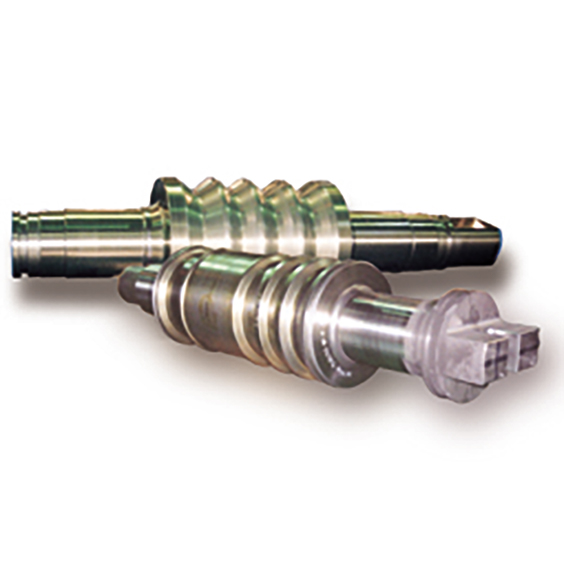
Reliable technologies backed by history Support provided for the entire process from raw materials to finishing
The SHI Group succeeded in the manufacture of ductile rolls for the first time in Japan in 1953. Since then, the SHI Group has secured and retained the strong position of the top manufacturer of ductile rolls.
Current product lines include cast iron varieties (ductile and glen cast iron), steel roll varieties (adamite and graphite steel), as well as high speed tool steel (HSS) rolls and powder high speed steel rolls, which are made available due to the improved performance of the rolling facilities, energy conservation, labor savings and improved productivity, in order to respond to a diverse range of our customers' requirements.
The SHI Group will continue to develop products that are suitable for the needs of the users.
Click here for detailed information about Cast Iron & Steel Rolls for Hot Rolling
Features
Special heat treated tough rolls: "SIP Roll"
A special heat treatment known as the "SIP" or the "Sumitomo Improvement Penetration" arranges the upper layer constituents of the roll surface in a precise manner, which not only improves the mass effect but also raises the overall strength and dramatically improves the bending durability. This is a roll with significant improvement of surface roughness resistance and thermal crack.
An example of mechanical characteristics
N treatment | SIP treatment | |
---|---|---|
Hardness (HS) | 45±3 | 45/50 |
Tension (kg/mm2) | 64 | 74 |
Bearing force (kg/mm2) | 49 | 58 |
Elongation (%) | 3.5 | 3.1 |
Impact value (kg/cm) | 0.9 | 1.6 |
Fatigue strength (kg/mm2) | 19 | 24 |
Fracture toughness value (KIc) | 185 | 203 |
Hardness distribution
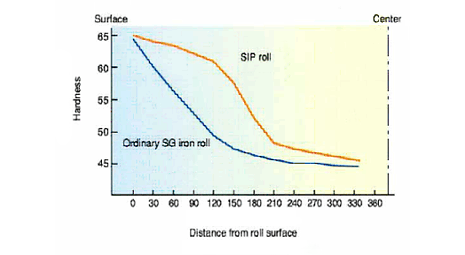
Sumitomo High Speed Tool Steel (HSS) Rolls: "STZ"
These are rolls that have properties that are in between the high speed tool steel materials and the conventional materials such as cast iron materials (ductile cast iron) and cast steel materials (adamite). These are rolls with material characteristics that appear to contradict each other, such as thermal crack resistance, toughness, wear resistance and surface roughness resistance, making it capable of responding to a variety of quality requirements as a raw material and through the entire process leading up to the finishing stand.
Image diagram of materials
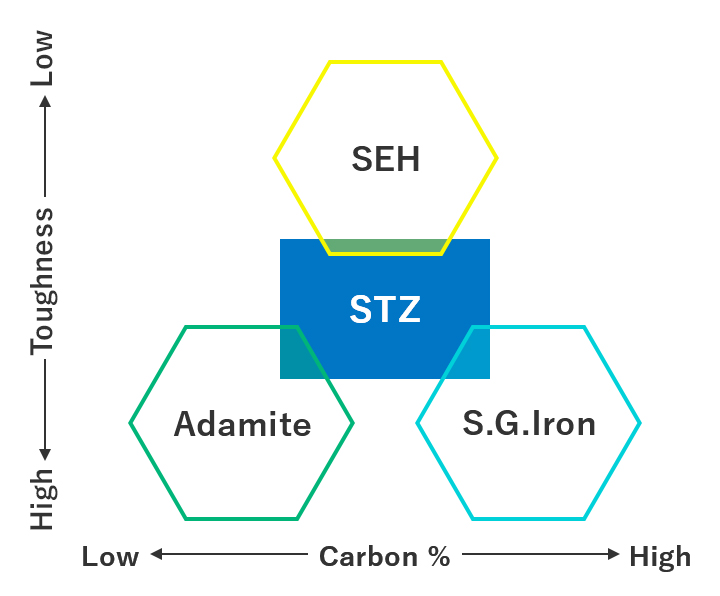
Friction test result
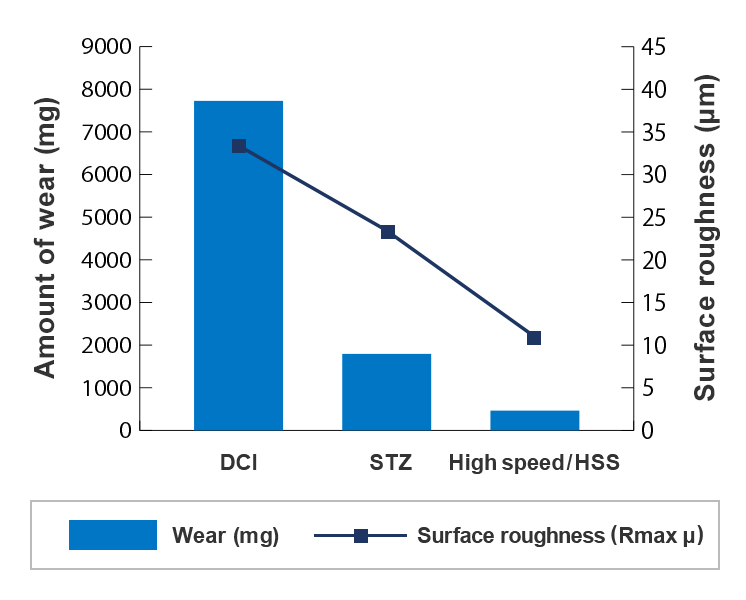
Sumitomo Powdered High Speed Tool Steel (HSS) Rolls: "SPH"
These products have better wear resistance and roughening resistance than soluble (casting) high speed tool steel rolls, and they are used as high-quality roll materials.
Positioning of Powdered High Speed Tool Steel
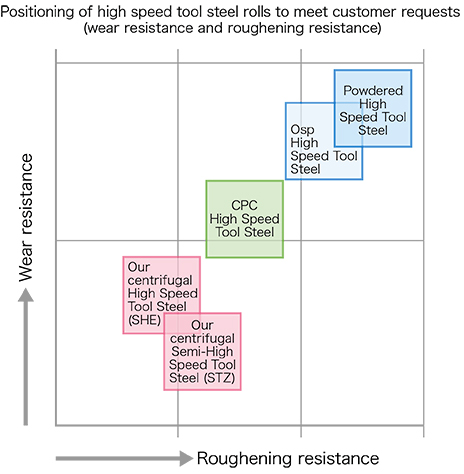
To each stand, we apply the manufacturing know-how of Osprey High Speed Tool Steel rolls (spray casting method: rapidly cooling and solidifying process in the Osp method) that we have manufactured previously. It is used for bar steel, wire rods, medium rolls for flat steel and rolls for finishing.
Comparison of Characteristics of Material Quality of High Speed Tool Steel Rolls
Type | Heat Crack Resistance Soluble High Speed Tool Steel | Medium Hardness Soluble High Speed Tool Steel | High Hardness Soluble High Speed Tool Steel | Powdered High Speed Tool Steel | |
---|---|---|---|---|---|
Stand to be applied | Improvement in wear resistance of the roughing stands | Improvement in wear resistance of the intermediate stands | Improvement in wear resistance of the finishing stands | Improvement in wear resistance of the finishing stands | |
Required quality | Heat crack resistance | ◎ | ○ | △ | × |
Roughening resistance | × | × | △ | ○ | |
Wear resistance | △ | ○ | ○ | ◎ | |
Ingredient design | Low alloy | Medium alloy | High alloy | High alloy | |
Heat treatment design | Hardening of the base structure | Hardening of the base structure | Hardening and control of the base structure | Hardening and control of the base structure | |
Microstructure design | Increase and decrease of hard carbide and carbide granular | Increase and decrease of hard carbide and carbide lumps | Increase and decrease of hard carbide and carbide lumps | Granular and finer structure, and hard carbide | |
Material quality symbol | SKN-2W | STZ-3W STZ-4W |
SEH-3W SEH-4W STM-5W |
SPH-20 SPH-30 |
|
Hardness Hs | 60/75 | 70/85 | 75/90 | 80/95 | |
Microstructure (x 500 times) |
![]() |
![]() |
![]() |
![]() |
Material Lineup
Type | Roll material | Material code | Hardness (HS) |
---|---|---|---|
Ductile rolls | Special heat treated ductile | SIP-3 | 40-55 |
Special heat treated ductile | SIP-4 | 55-60 | |
Special heat treated ductile | SIP-5 | 60-65 | |
Special heat treated ductile (wear resistance) |
BSIP-3 | 50-60 | |
Special heat treated ductile (wear resistance) |
BSIP-4 | 55-65 | |
High alloy ductile | 73A | 50-65 | |
High alloy ductile | 73B | 60-70 | |
High alloy ductile | 7LB | 70-80 | |
Indefinite chilled rolls | Indefinite chilled | 64 | 60-70 |
Indefinite chilled | 65 | 65-75 | |
Indefinite chilled double poured | 64W | 65-75 | |
Indefinite chilled double poured | 65W | 70-80 | |
High Grain | H65W | 75-85 | |
Adamite rolls | Special heat treated adamite | SIP-2A | 35-50 |
Special heat treated adamite | SIP-3A | 40-55 | |
Special heat treated adamite | SIP-4A | 50-60 | |
Special heat treated graphite steel | SIP-2G | 35-45 | |
Special heat treated graphite steel | SIP-3G | 40-50 | |
Centrifugal cast adamite | SIP-4AW | 50-60 | |
Centrifugal cast adamite | SIP-5AW | 55-65 | |
Forged adamite | SIP-X | 40-65 | |
High Speed Tool Steel rolls | Centrifugal cast high speed tool steel (heat crack resistance) |
SKN-2W | 60/75 |
Centrifugal cast high speed tool steel | STZ-3W | 70/80 | |
Centrifugal cast high speed tool steel | STZ-4W | 75/85 | |
Centrifugal cast high speed tool steel | SEH-3W | 75/85 | |
Centrifugal cast high speed tool steel | SEH-4W | 80/90 | |
Centrifugal cast high speed tool steel (wear resistance) |
STM-5W | 80/90 | |
Powder High Speed Tool Steel rolls | Powdered High Speed Tool Steel | SPH-20 | 80/90 |
Powdered High Speed Tool Steel | SPH-30 | 85/95 |
For detailed information about the products please contact
Phone
Sumitomo Heavy Industries HIMATEX Co., Ltd.
Web
Sumitomo Heavy Industries HIMATEX Co., Ltd.