CFB Scrubbers
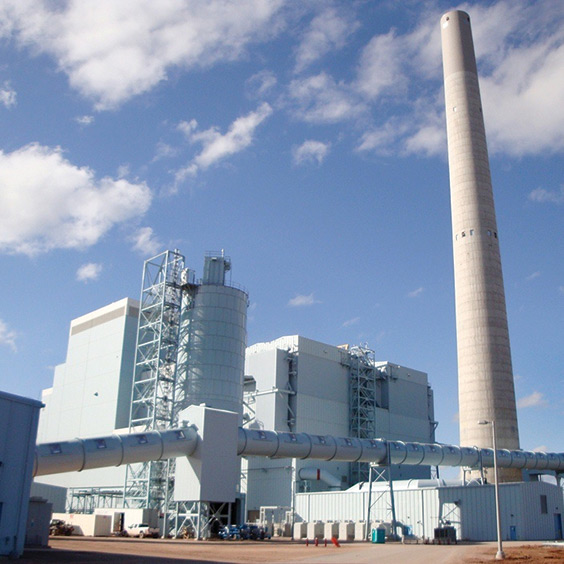
High-Value Multipollutant Emission Control Solutions
Emission limits for pollutants like SOx, NOx and particulate matter continue to tighten for power plants and industrial facilities worldwide. Acid gas and heavy metal emissions, such as of HCl, HF, and Hg, are a major concern as well.
The Circulating Fluidized Bed Scrubber (CFB Scrubber, CFBS) is a an efficient and flexible flue gas cleaning (FGC) technology for removing a wide array of pollutants from flue gases from almost any combustion and industrial process. The technology has been applied widely in power plants, steel mills, refineries, waste-to-energy plants, combined heat and power plants, and plants in many other industries. It has been demonstrated over a range of flue gas flow rates from small industrial boilers to large power plants with capacities over 500 MWe.
Features
- 1Control SOx, acid gases, heavy metals and particle emission in a single unit
The CFB scrubber reduces SOx, particulate matter (PM10 and PM2.5), acid gases (HCl, HF), mercury (Hg) and organic compounds (dioxins and furans) emissions in the same unit. The semi-dry process utilizes mainly hydrated lime as absorbent, with a minimal amount of water sprayed. Activated carbon can be included if needed.
- 2Scalable solution for large plants, compact footprint
Our CFB scrubber technology is a proven technology on a large scale, with single-unit designs up to 500 MWe and with fuels of sulfur content above 4%. Multiple parallel venturis in the absorper bottom allow single absorber designs for up to 800 MWe. Absorber is cylindrical and reaction residence time is provided by the unit height, providing for compact footprint.
- 3High capture efficiency with low water consumption
The semi-dry CFB scrubber technology utilizes typically 40-50% less water than wet flue gas desulfurization (FGD) units. Due to the excellent mixing properties of the CFB design, combined with long solids residence time of 20-30 min, the sorbent consumption is minimized. The key process advantages of this technology are the following:
- In combination with CFB boilers, the semi-dry process takes advantage of unreacted calcium of the fly ash, reducing or even eliminating the use of lime.
- Lime injection is not limited by incoming flue gas temperature, because spray water is used to condition the process into optimal temperature.
- Due to absence of slurry, CFBS process utilizes low quantity of water, and the scrubber byproduct is solid, eliminating the need for wastewater treatment.
- 4Benefits in investment and O&M costs
The CFBS technology can have several cost advantages over wet FGD (flue gas desulfurization) technology:
- The investment costs for a CFB scrubber are often 25 - 50% lower than wet FGDs for the same plant size.
- CFBS can have overall advantage in operating costs (OPEX) over wet FGD when fly ash components can be utilized as sorbent.
- Water consumption is lower, and often also power consumption is lower.
- The byproduct can often be used as a cement additive, general aggregate or landfilled.
- Maintenance costs and needed annual downtime are very low in CFBS technology due to utilizing practically dry material (no lime slurry) with low erosion and negligible corrosive properties, and due to featuring only easy to maintain auxiliaries.
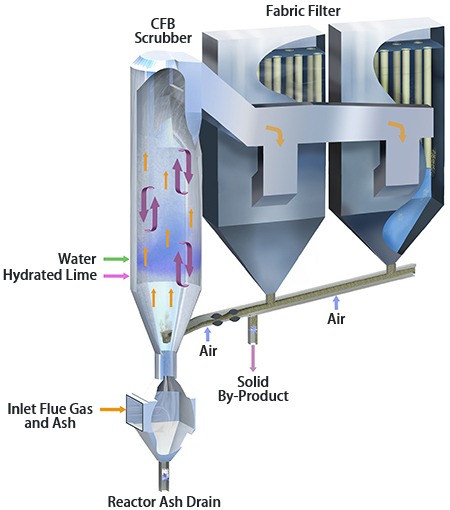
For detailed information about the products please contact
Phone
Sales Department, Energy & Environment Group
Web