Customers
Basic Views
The corporate mission of the Sumitomo Heavy Industries (SHI) Group is to contribute toward the development of society through provision of excellent products and services. We firmly believe that gaining long-term trust from customers around the world will lead to sustainable growth for the SHI Group, increase its corporate value, and allow us to meet the expectations of all stakeholders.
To ensure our continued provision of quality products and services that afford customers in diverse industries satisfaction and reassurance in their use, we have developed a quality assurance system suitable for each product, observe work processes based on the system, manage our product quality, and strive to make further improvements.
Quality Principles and Policy
- Quality Principles
- Through the continuous and unwavering pursuit of world class quality that is recognized globally, we will supply customers with products and services that they recognize as adding value to their business.
- Quality Policy
-
- Customer First:
Define quality targets based on the expectations of the customer - Continuous Progress:
Continuously advance the quality system and incorporate quality with a process mindset - Everyone Participates :
Every person involved in quality sets an objective and tackles quality issues head on as a team
- Customer First:
Quality Assurance System
Each division and affiliated company of the SHI Group has its own quality assurance systems that are suitable for its business contents. Furthermore, the quality assurance department of each division and affiliated company reports directly to the division general manager or affiliated company president, to ensure its independence. The Corporate Quality Group of SHI's Head Office exercises overall control over the SHI Group in terms of product quality.
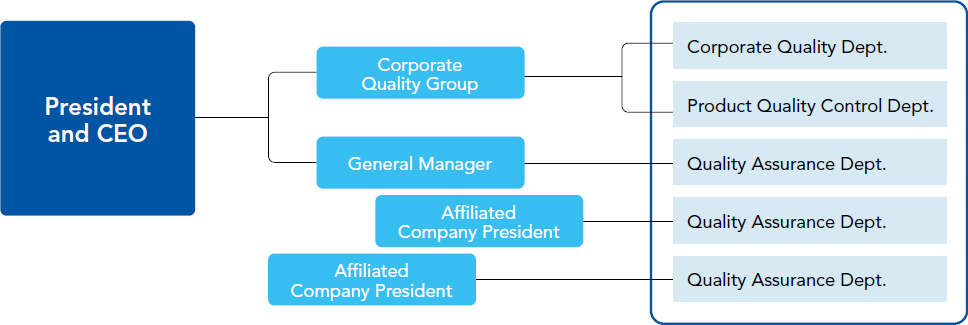
Initiatives
- Process review
- This is an occasion on which the President and CEO of SHI visits each division and affiliated company to review its work processes. Starting with a review of the manufacturing site, the President and CEO of SHI / an officer at the Head Office holds detailed discussions, based on quality issues and manufacturing issues as main themes, with the responsible person of the relevant division about problems with processes and improvements to be made therein.
- Quality assurance department managers meeting
- This is a meeting hosted by the Corporate Quality Group of SHI's Head Office and attended by the quality assurance department managers of divisions and affiliated companies. It is aimed at enabling these managers to share ideas, policies, and measures for improving quality, learn from each other, and thereby enhance their organizational ability. Continuous and diversified discussions are held on the theme "From strengthening of recurrence prevention activities toward proactive activities." In addition to exchanging information about quality on a monthly basis, we continuously monitor using the "Customer Satisfaction Indicator (KPI)" in order to understand the relationship with customers from a quality perspective. We also hold regular discussions to improve the KPI.
- Quality Management System (QMS) audit
- This is an action taken by the Corporate Quality Group of SHI's Head Office to verify the effectiveness of quality management systems. The SHI Group deals with a wide range of product, and there is a quality assurance system for each operating division and product according to its circumstances and operations. Through verification of the dissemination processes of quality manuals, quality regulations, documented procedures, and quality records, this audit verifies the effectiveness of a quality management system and the capability of each process.
ISO 9001 certified: 95% of the major manufacturing sites (as of the end of FY2023)
- Introduction of "Six Sigma" and provision of training
- We have introduced Six Sigma as a common quality improvement tool for the Group since 1999, and have continued to provide practical training on process improvement. We are working to strengthen our processes by training and assign "Master Black Belts" to supervise process improvement at business divisions and affiliates, "Black Belts" to take charge of solving difficult problems and provide guidance for problem solving, and "Green Belts" to take charge of problem solving at workplaces as project leaders.
As of the FY2023, the total number of certified Green Belts has exceeded 2,497, and the total number of certified Black Belts has surpassed 201, aiming to elevate the overall level.
- Promotion of Product Security Activities
- We strive to improve product quality in accordance with the following basic policy.
- The Sumitomo Heavy Industries, Ltd. Group (hereinafter referred to as “the SHI Group”) recognizes that ensuring the security of its products and services is a critical management priority, directly linked to reducing customer risk and ensuring safety. To enable customers to use its products and services with confidence, the SHI Group is committed to implementing, maintaining, and continuously improving the following initiatives.
- Compliance with Laws and Regulations
- All executives and employees shall comply with applicable laws, regulations, contractual obligations, and other relevant requirements related to product security.
- Establishment of a Product Security Management Framework
- The SHI Group shall establish and maintain a management framework to effectively promote and oversee product security initiatives.
- Implementation of Product Security Measures
- To prevent or minimize damage caused by unauthorized access or other threats to the confidentiality, integrity, availability, and other critical attributes of its products and services, the SHI Group shall implement security measures throughout the product lifecycle. These include embedding security into the design and development phases, providing vulnerability information related to its products and services, and conducting regular security assessments as appropriate.
- Incident Response
- In the event of a product security incident, the SHI Group shall promptly notify customers and relevant stakeholders of appropriate countermeasures through suitable communication channels. Subsequently, root cause analysis and corrective actions shall be undertaken to prevent recurrence.
- Education and Training
- The SHI Group shall provide product security education and training to executives, employees, and, as appropriate, business partners, to foster continuous improvement in product security awareness and practices.