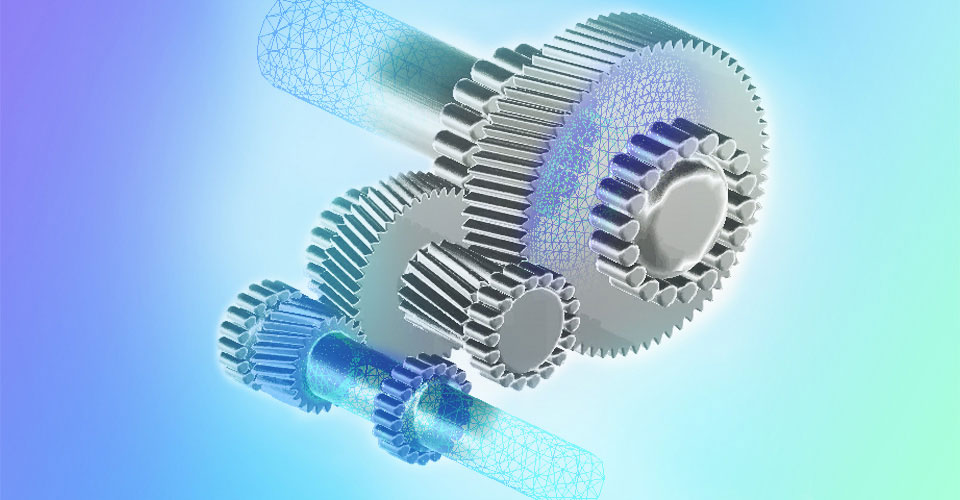
Supporting Development with Innovative Simulation Technology: RMD and MBM
The Technology Research Center of Sumitomo Heavy Industries’ (SHI) Corporate Technology Management Group supports development of a wide range of products by offering technology for simulating structures, vibrations, and thermal hydraulics. This independently developed technology continues to evolve today.
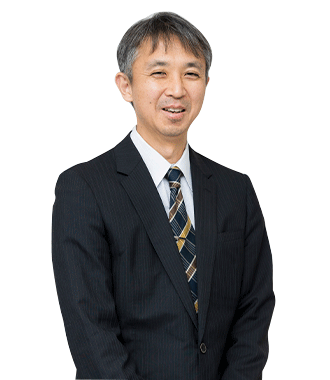
Solution Technology Dept.
Technology Research Center
Corporate Technology Management Group
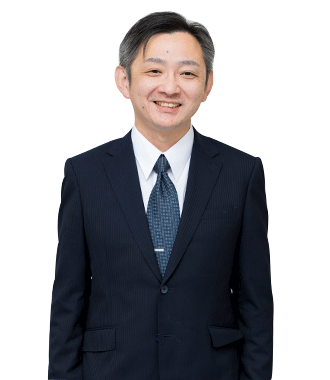
Solution Technology Dept.
Technology Research Center
Corporate Technology Management Group
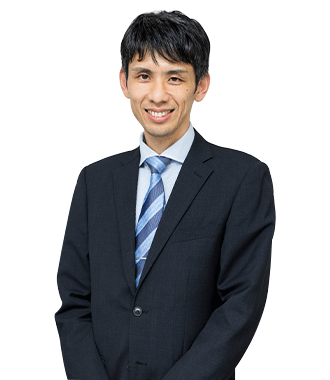
Technology Research Center
Corporate Technology Management Group
“Renormalization Molecular Dynamics” (RMD) has made simulation practical
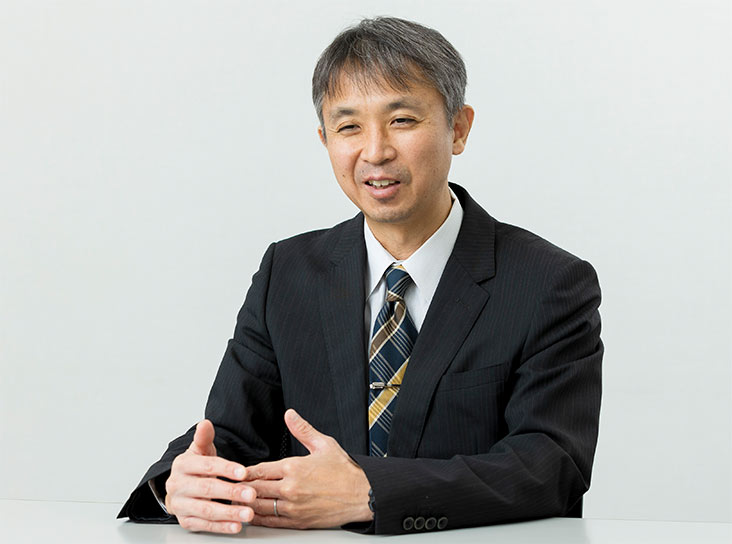
When General Manager of Technology Research Center joined SHI as a researcher, no one in the company could handle molecular dynamics (MD), a method for computer simulation of the physical motions of atoms and molecules. MD is an outstanding simulation technique that allows handling of solids and liquids in states far from equilibrium.
“After joining SHI, I went to university for training to brush up on MD, but I still wasn’t able to handle MD for about five years after I came back. MD can only handle scales up to nanometer units, so it had a reputation inside the company of being interesting but unusable. Something was lacking to make it practical.”
It was at that point that the superior of the General Manager at the Technology Research Center at the time, developed renormalized molecular dynamics (RMD) by applying renormalization theory to MD. The superior derived the calculation formulas, and General Manager of Technology Research Center and his fellow researchers started out in the role of system operators.
The basic idea of RMD is to refrain from exactly solving for micro phenomena, and to “renormalize” to macro phenomena. This enabled simulation of macro scale phenomena.
MD requires huge amounts of computing time, so calculation costs have been an issue for many years. According to General Manager of Technology Research Center, solving this problem led to dramatic improvements in development support, accuracy of problem handling, and speed.
“We focused on the numerous problems that couldn’t be calculated with commercial software. The most typical were the gears of gear reducers, and injection molding machines. Theoretically, these contain small parts so difficulty is high, but our method can even handle hydraulic excavators. It wasn’t so much trouble for me. The one who really struggled was The superior who derived the formulas for RMD. I was able to adapt a technique with established theory into something closer to practical needs in the field.”
Rapid advances in research are meaningless if they’re not useful for the company. So General Manager of Technology Research Center went to the divisions, and shifted to a more practical research footing.
“There were people in our divisions who took an interest in the research. Even when the software was full of bugs, they hung in there and didn’t get discouraged. As a result, it became possible to do more practical three-dimensional computer simulations. Today I can affirm with confidence that this is a practical useful technology.”
Assume, for example, that we have an equation on the right and an equation on the left. We perform iterative calculation until the values on both sides match, but if the values diverge, they will never converge, and the calculation will continue forever without ending. However, when RMD is used, the calculation never diverges, and the phenomenon of failure to converge never occurs.
“Previously, there was no analysis method that guaranteed contact accuracy through functional approximation of surface shape. Going forward, we want to continue evolving our company’s unique technologies, which are beyond the ability of other firms to imitate.”
Solid research results have garnered recognition, and appeared in academic journals with international significance
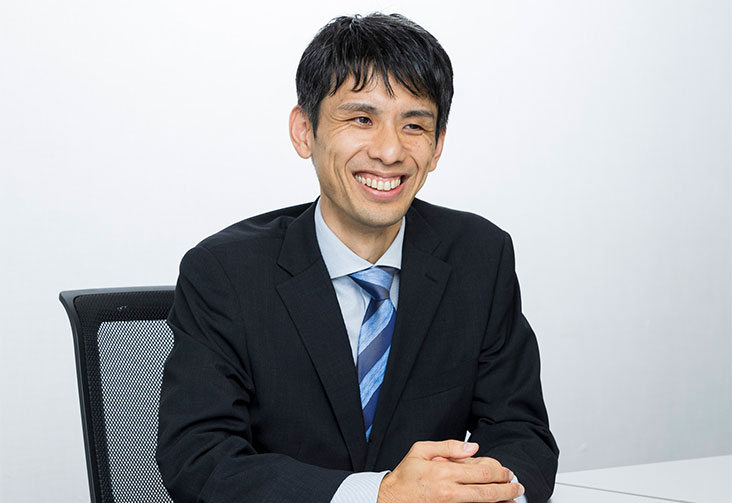
Our researcher Engineer of Technology Research Center enabled macroscale analysis of polymers by using the theory of RMD.
“When I first joined the company, I helped solve problems relating to the gears of gear reducers by using an RMD simulator developed by my superior, General Manager of Technology Research Center. However, as the range of application broadened, I got involved with development of polymer materials. Polymers have particles connected like beads on a string. As materials, they have properties like viscosity and elasticity. By applying the technique of renormalization to the molecular dynamics of polymers, we successfully developed RMD for polymers.”
Engineer of Technology Research Center wanted people to use polymer RMD with actual machines, so he focused on developing an application to a device called a kneader.
“A kneader is a machine that kneads together polymer materials with two blades. In our divisions, there are employees known as ‘artisans,’ and they developed blades for superior kneading. There are many unclear points about why blades knead well, and I’m working with the divisions to develop indicators of the degree of blending.”
Here too, in-house cooperation of divisions is essential. Getting them to cooperate requires not just sparking their interest, but also powers of persuasion.
“I do development together with divisions, but I also had a lot of worries. That’s because it takes one or two months to do one analysis. My worries intensify while I’m waiting, wondering whether the results will come out correctly. I don’t want to cause trouble for the employees of the divisions, so there’s pressure.”
Even when results weren’t immediately forthcoming, the divisions steadfastly supported Engineer of Technology Research Center’s research.
“I can’t really say our previous collaborations with divisions have gone smoothly. It’s because we hadn’t fully built up the relationships to enable cooperation. I keenly realized that, to do R&D, you need to search out employees in the divisions who will cooperate with you in earnest.”
Research results on RMD have garnered recognition, and in 2021 an article appeared in Scientific Reports, published by Springer Nature. This paper showed the correctness of applying RMD to three problems: calculation of the collision of macroscopic elastic spheres, calculation of a phase transition due to latent heat, and mesoscale calculation near the critical point.
“The article was written by The superior and Mr. Matsumura—previous group leaders at the Technology Research Center who developed the foundations of the theory. Mr. Matsumura lived abroad when he was younger, so he had no problems writing the paper in English, but there were multiple reviews before it was published. Publication led to wide recognition of our research results, and that gave us greater credibility. Researchers all over the world saw our results, and we were thrilled because we could prove, within the company, that we aren’t doing dubious research (laughs).”
Actually, the article was rejected twice before it was published. The authors had to reexamine the points critiqued by the reviewers, resolve those problems, and prepare a foundation and theory whose content was 100% correct.
“I think it was really tough for Mr. Matsumura. Because he was always investigating where the problems were. Thanks to publication of the article in Scientific Reports, the renormalization theory has garnered attention from all over the world, and it has given us pride in our work.”
Engineer of Technology Research Center recalls many notable points in the course of events leading up to publication of the article.
“The important point in research is that it’s more about people than technology. If you do the research you think is interesting, but no one wants it, it’s just self-gratification. It’s important to take the initiative, listen to the problems of the divisions, and consider how the develop the research. If a calculation takes a few months, the other party may not be willing to wait. That’s an issue we’ll have to address going forward.”
What’s the “ultimate goal” that only SHI can achieve?
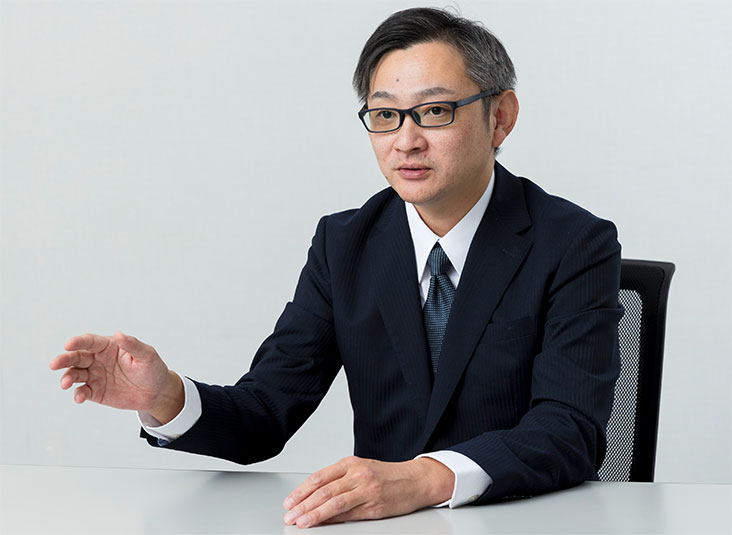
SHI also has a unique simulation technology called the “magnetic beads method” (MBM). Researcher Senior Engineer of Technology Research Center explains:
“The magnetic beads method (MBM) is a magnetic field design and development tool for equipment like motors, magnetic shields, and magnetic gears. It's a magnetic field analysis technique requiring no spatial mesh, thereby enabling analysis of large-scale three-dimensional shapes. Since no spatial mesh is needed, the method allows magnetic field analysis while taking into account device movement and deformation. Analysis can also be done at points far away from the device. These abilities set the technique apart from other methods.”
Senior Engineer of Technology Research Center began developing MBM as part of efforts to downsize and increase output of devices. As devices were downsized, analysis had to be switched from two to three dimensions. Senior Engineer of Technology Research Center was originally a designer, but his superior persuaded him to take up magnetic field analysis.
“It was tough. At the time, PC performance was poor, and calculations always took a long time. For a time, I moved away from MBM development. I was thinking of returning to it before my retirement, but higher CPU performance and GPGPU technology reduced computing time. So I resumed development, and we finally reached a level where the technique was usable for designing actual machines.”
Senior Engineer of Technology Research Center resumed development 10 years ago, and as result of increased speed and other improvements, took the method to a level enabling use in design of actual machines. Achievement of practical use is a great moment where one feels meaning in work as a researcher.
“After I joined the company, I belonged to a motor development team. My superiors and younger colleagues from those days now have leadership positions in the divisions. The fact that my old colleagues are doing design with a tool I made gives me a sense of worth and pride. When they say things like ‘You’ve made our jobs easier,’ it makes me really glad that I developed it.”
When design was done in two dimensions, there was sometimes deviation between the design and results. MBM is a revolutionary system that enables design in three dimensions, thus ensuring a match between design and results. One major objective at present is deploying these simulation technologies throughout the entire SHI Group.
“If the producing side doesn’t actively sell the idea, it won’t really catch on in-house. The other person may be satisfied with the current approach, so it’s important to persuade them by clearly explaining the advantages of adopting the new system. In that sense, I think building human relationships with division employees is also an important element.”
Going forward, the Technology Research Center will continue research to elucidate phenomena and achieve optimization. To conclude, General Manager of Technology Research Center spoke of his dreams.
“Our ultimate goal is to realize an optimization system—incorporating a modeler with a high degree of freedom, and high-accuracy high-speed MBM—which automatically generates optimal shapes that human beings can’t think up. That will allow us to deliver better products to the world simply by waiting for innovation to occur inside a computer. However, creating such a system requires the wisdom of human beings. We must always have our antenna out for that. That’s the ultimate dream to shoot for because we’re the ones who developed MBM in-house.”
He says that a “sequel” is planned for the previously mentioned article on RMD. Also, machines and parts will continue to evolve in the future, and that’s only possible thanks to our researchers. As long as the people are there, research and development will continue forever.
Analysis of Gears using Renormalized Molecular Dynamics
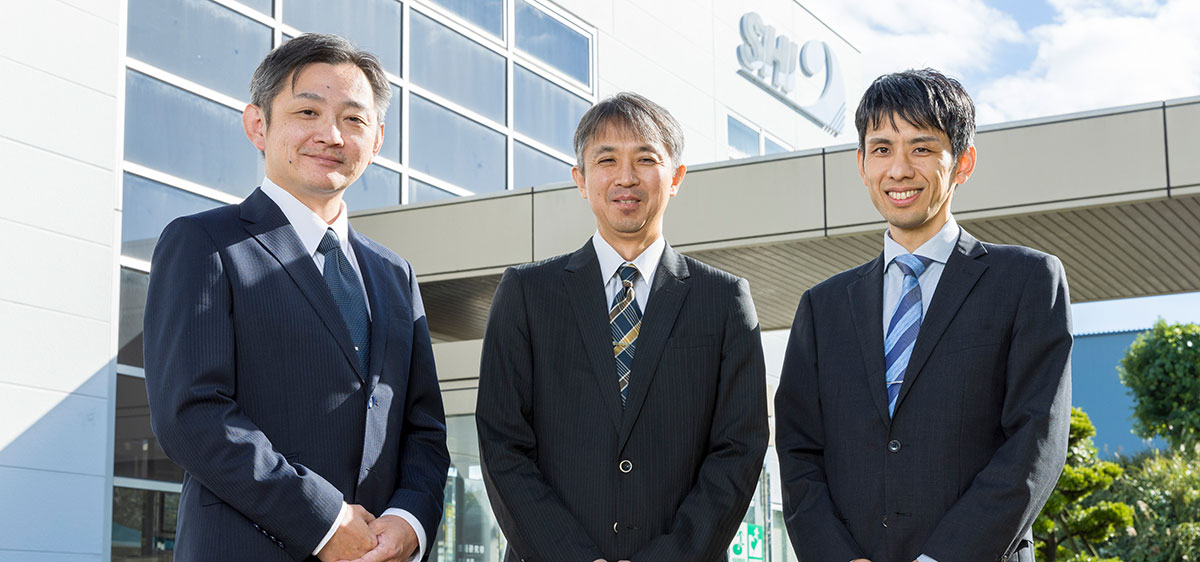
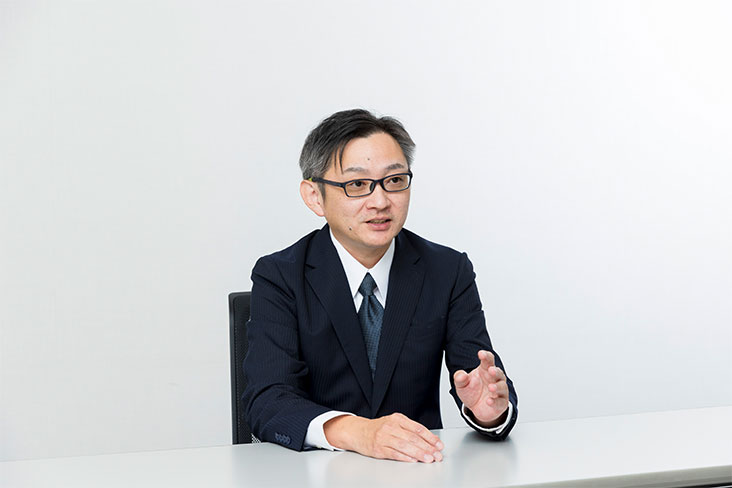
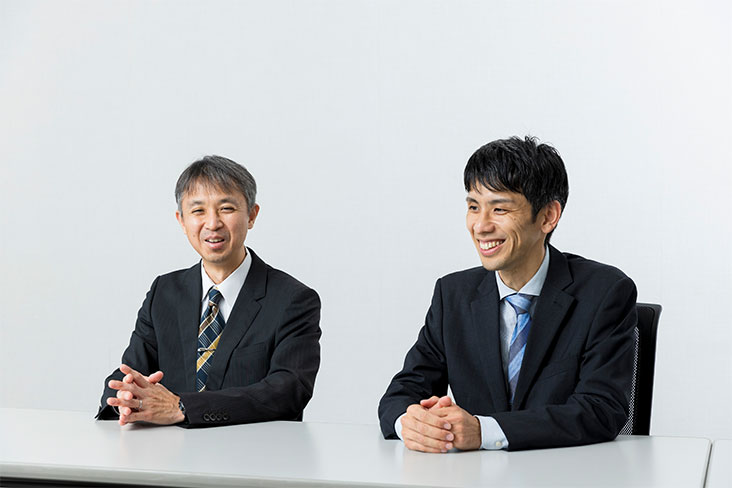
SHI Pride
- Vol.1 A Clear View of the Distant Heavens
- Vol.2 Cures without Surgery: Advanced Cancer Treatment
- Vol.3 Exploring the Mysteries of Space
- Vol.4 Dramatically Changing Quayside Cargo Handling
- Vol.5 Cyclo Drives Continue to Evolve
- Vol.6 The Steam Turbine - Protecting the Environment and Advancing Society
- Vol.7 Persistent Determination to Reduce Defects, Losses and Faults to Zero
- Vol.8 Treating Cancer through the Use of Neutrons - A Compact Accelerator Opens the Door to Widespread Use -
- Vol.9 Automated storage system with unrestricted movement, for transforming the future of the logistics industry
- Vol.10 Anaerobic Wastewater Treatment and Biogas Power Generation System using Ume Seasoning Effluent bringing Recycling-Friendly Society
- #01 Technology that has the potential to dramatically change automobile frame manufacturing STAF created by maintaining a comprehensive customer perspective
- #02 The ECY Series:A smaller Gear reducer after over 10 years of development
- #03 Cancer Therapy System "Boron Neutron Capture Therapy (BNCT system)"
- #04 Supporting Development with Innovative Simulation Technology: RMD and MBM