Notice Regarding the Completion of a Test Unit for the Steel Tube Air Forming (STAF) Production System which Achieves Significant Weight Reductions in Automotive Body Frames
September 28, 2017
Sumitomo Heavy Industries (President and CEO: Shunsuke Betsukawa; hereinafter referred to as “SHI” or the “Company”) celebrated the completion ceremony of a test facility for its “STAF” automotive body frame production system, which the Company has been developing for some time, on September 20, 2017.
STAF, which stands for Steel Tube Air Forming, is the new forming process system whereby a steel tube that is set in the mold of a press machine goes through the process of “resistance heating → high pressure air injection → forming → hardening”. This makes it possible to perform the integrated forming of the frame and the flange, component that is essential for frame assembly. Unlike the traditional method of welding two sheet metal, the STAF system improves rigidity and simplifies the overall production process. Moreover, by increasing the rigidity of the frame, it makes it possible to use thinner materials, thus achieving an approximately 30% reduction in the weight as compared to traditional manufacturing methods.
SHI has already commenced discussions with automotive manufacturers on the topic of adopting STAF for use in producing automotive components with the aim to introduce the system in this field during FY2018. The Company has positioned STAF as a key growth area for the future and has set a sales target of JPY10 billion by 2024.
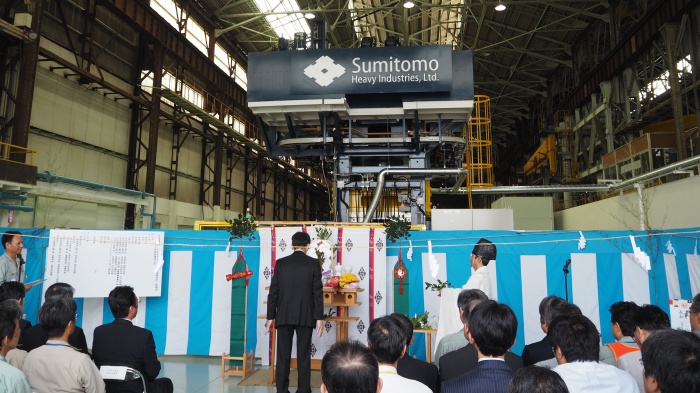
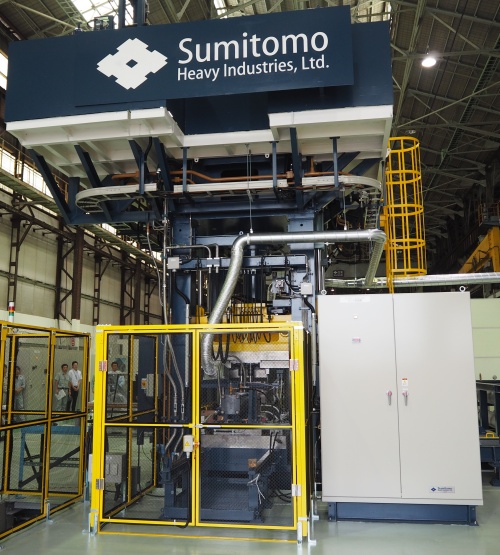
1.Resistance Heating
After the steel tube is set on the mold, a resistance current is passed through to heat the metal. By doing so, the tube is heated to around 900°C within 10 seconds. With resistance heating, the right and left electrodes have the same contact area against the tube, making the contact more stable than in the case of sheet metal, enabling homogeneous heating. Furthermore, compared against the furnace heating method, it achieves significant reductions in power consumption.
2.Flange Forming
After resistance heating, the mold closing position (in a half-open state) is adjusted and high pressure air is supplied to the area. The mold is then closed while the half-open part is slightly expanded to form the flanges.
3.Die Quenching
After closing the mold, more high pressure air is supplied to the area for blow molding so that the shape of the main body becomes similar to that of the inner surface of the mold. Since the material is closely attached to the metal mold, it can be rapidly cooled to have a high tensile strength of approximately 1,500 MPa.
1.30% Reduction in Weight
Given the continuous closed cross-section structure of the ultra-high strength material, it can be made it to highly-strong, highly-rigid components. As a result, it is possible to reduce the thickness of the tube. Under the same strength parameters, if the STAF production system replaces traditional methods of producing automotive components, it will be able to achieve an approximately 30% reduction in overall weight.
2.Cost Reduction
The STAF production system eliminates the need for blanking1 and trimming2, which are required for press forming with sheet metal. In addition, only end cutting is required after forming which means that the yield can be increased to around 90%. At the same time, given that the flanges are already formed along with the tube, the number of required components can be reduced, thereby achieving a significant reduction in overall production costs.
3.Simplified Production Process (Low Investment Cost / Space Saving)
When closed cross-section structure components are formed using sheet metal, five machines are required for blanking, heating, pressing, trimming and welding. On the other hand, the STAF system combines the heating and pressing process into one step after pre-forming, and before end-cutting. As such, only three machines are required meaning that the production process can be simplified.
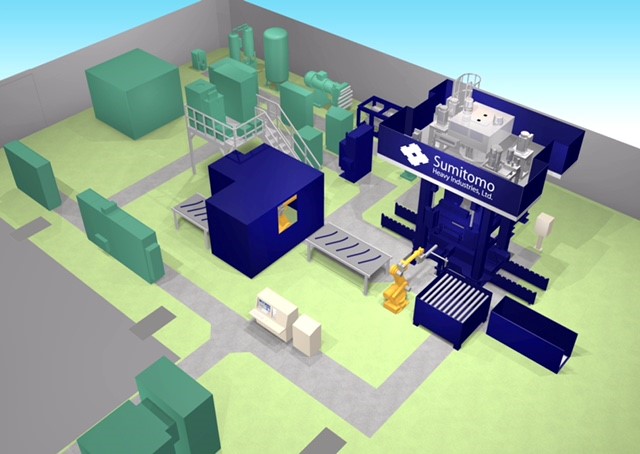
4.High Productivity
While hot stamping uses four processes to form a closed cross-section structure, the STAF process reduces the number of processes to two by eliminating heating and welding. Through the significant reduction in the number of indirect steps during the process, the productivity can be increased.
Note 1: Blanking is a metal fabricating process during which the material is punched to form contours.
Note 2: Trimming is a metal fabricating process during which unnecessary parts of the edge or weld of sheet metal or forged products are cut off.
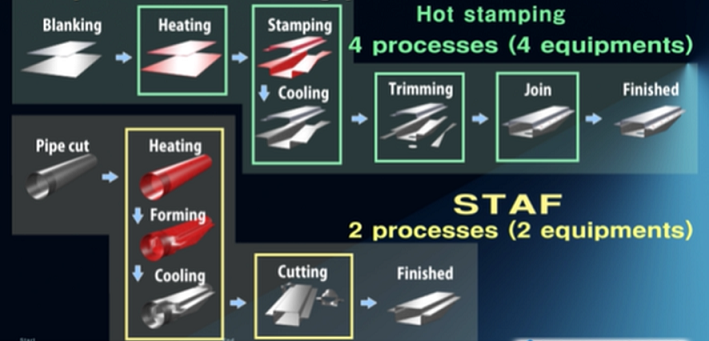