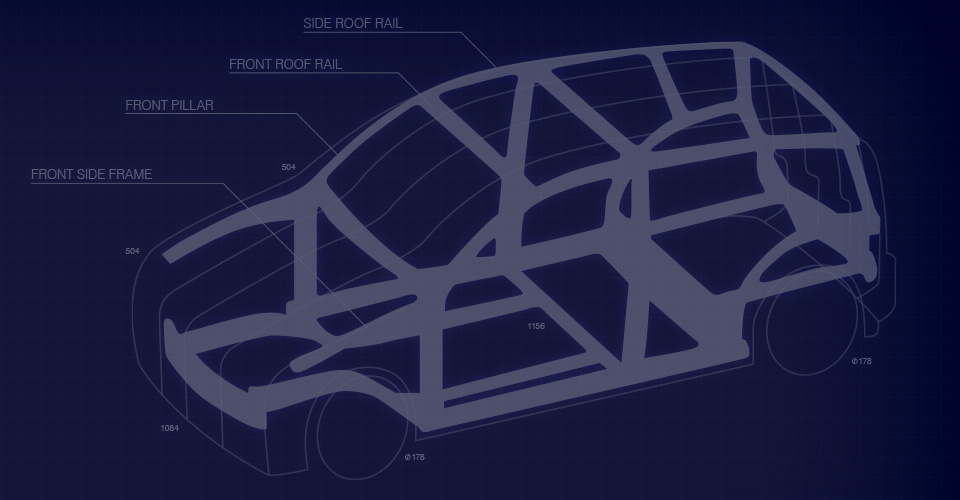
自動車フレーム製造を
一変させる画期的な技術。
徹底した顧客視点が
「STAF」を生んだ。
鋼管をプレス機で押し固めてつくられる自動車フレーム。
バリを取ったり、接合部品を後から溶接する工程がこれまでは不可欠だった。
その手間を省き、材料の軽量化につなげる画期的な技術「STAF」。
その開発プロジェクトが大切にしていたこととは──。
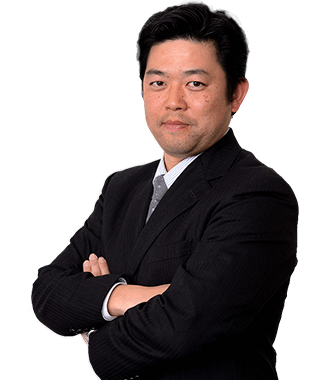
主任技師
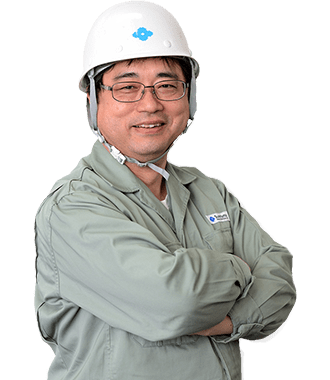
主任研究員 博士(工学)
いま車に求められるもの
低燃費と安全性の両立
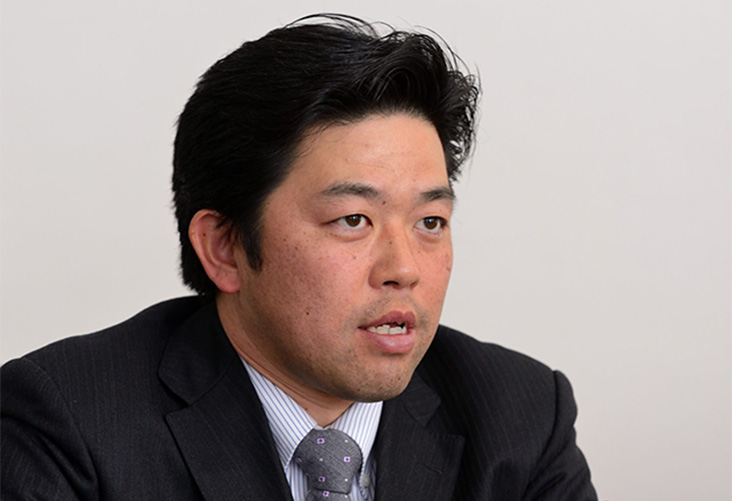
自動車に今求められるのは、さらなる低燃費などの環境性能と軽量化だ。車体が軽くなれば、それだけ燃費も小さくなる。ただ、材料を軽くして剛性を失えば、もう一つの課題である安全性を損なう。一挙両得とはなかなか行かないジレンマ。しかし、社会が自動車に求める環境基準はますます厳しくなる一方だ。自動車業界にとっては、より軽くて安全な車を作るための製造方法のブレークスルーが、待ったなしに求められている。
例えば車体を支える鋼鉄製のフレーム。鋼板を金型プレス加工して作るのが一般的で、板金プレス加工やホットスタンピングなどいくつかの方法が用いられてきた。ただ、軽量化が難しい、工程や設備が複雑になるなどの課題を抱えていた。
そこに登場したのが、住友重機械工業が開発した「STAF」である。「Steel Tube Air Forming」の略称で、パイプ状の鋼管に高電流を流して加熱し、さらに高圧空気でブロー成形すると同時に焼入れする方法だ。フレームを組み立てる際に不可欠のフランジと呼ばれる鍔(つば)状の部品を、フレームと一体で成形できる。つまり、フランジを後から溶接で接合する必要がないため、剛性が向上し、工程も簡略化できる。この製法でフレームの剛性が高まるということは、軽量化できるということ。工程がシンプルにできるということは、つまり製造コストの低減に直結するのだ。
技術研究所のシーズをプロダクトとして世に出すという仕事
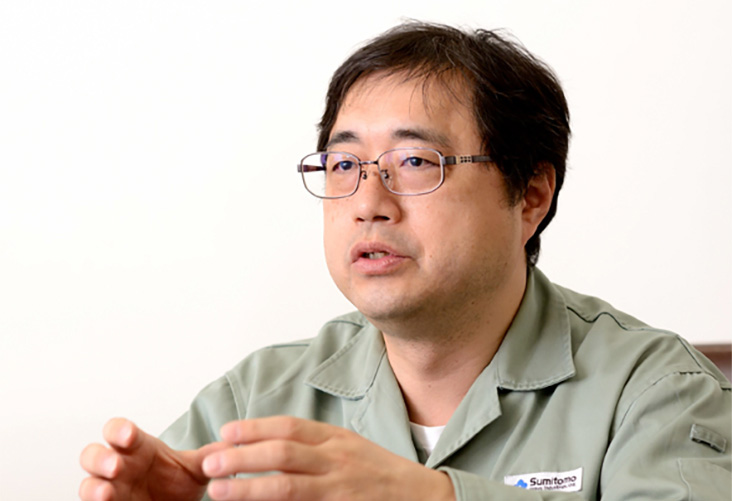
「車体フレーム製造工法については、当社は後発。しかしこの分野に進出することは、海外からの技術追い上げをかわすためにも必須の課題で、当時所属していた技術研究所で基礎研究を始めました。2011年の東京モーターショーである技術ベンチャーと知り合い、その勉強会に参加しながら、車載部品技術の知見を蓄えていきました」と、企画本部経営企画グループ・主任技師は振り返る。
勉強会に同席していたのが、大手自動車メーカーでの技術研究所の経験がある技術コンサルタントの小松隆氏だ。企画本部経営企画グループ・主任技師はある会合で小松氏が呟いた一言を聞き逃さなかった。「軽量化を果たすためには、高圧空気を送り込んで、フレームとフランジを一気に成型する方法があるのだが……」。それがSTAFだった。アイデアはあったのだが、どこの企業もその開発に成功していない。
住友重機械工業にできるかどうかはわからない。ただ、挑戦してみる価値は十分にある。企画本部経営企画グループ・主任技師らは早速、社内を説得して回った。技術研究所のシーズをプロダクトとして世に出すという自身の使命を達成したかった。
2013年、技術研究所内にSTAFプロセスの実証プロジェクトが立ちあがり、産業機器事業部のプレス設計グループにも応援を頼んだ。2015年からは新居浜に場所を移し、実証実験が繰り返された。スミメックエンジニアリングなど設計子会社からも専門の技術者を呼び込んだ。総勢8名と少数精鋭ながら、世界で誰もやったことがないエンジニアリングへの挑戦にメンバーは心躍らせた。
「最も難しかったのは、材料の特性や金型設計を含む成形条件の検討です。当初は一つの形状の成形で、200回以上の試験を繰り返しました。なんとか技術的に可能というメドは立ったのですが、これだけでは駄目。お客様である自動車部品製造会社にとって使いやすい装置に仕上げなければなりません。技術に加えてマーケット的なセンスも同時に求められるのです」
と、企画本部経営企画グループ・主任技師を補佐しつづける技術研究所材料技術グループ・主任研究員は言う。研究開発者に求められるのは徹底した顧客視点。これは企画本部経営企画グループ・主任技師 が常日頃、口を酸っぱくして語っていたことでもあった。
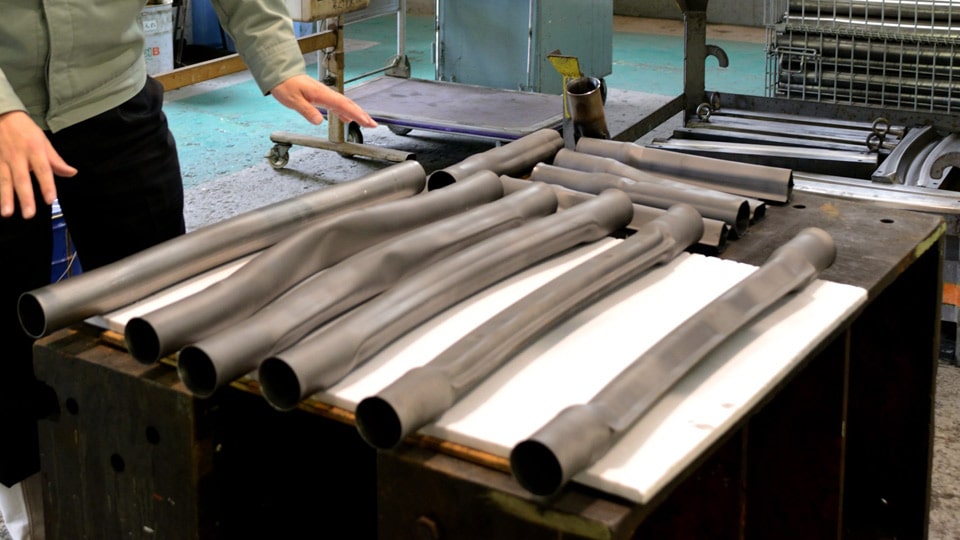
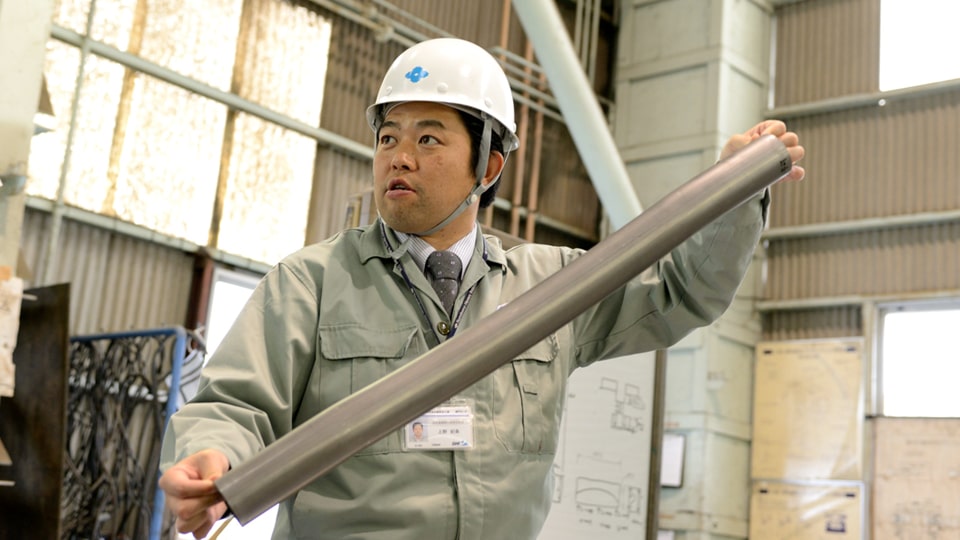
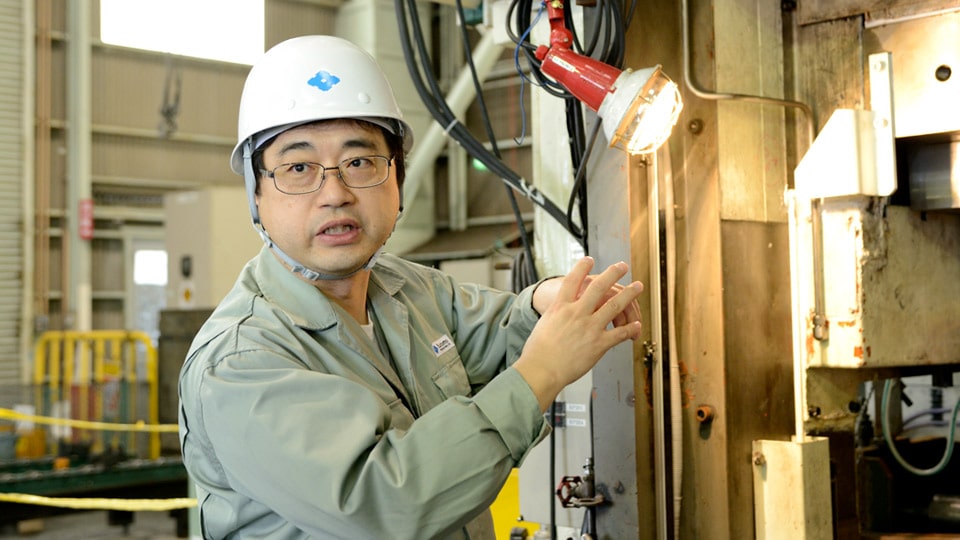
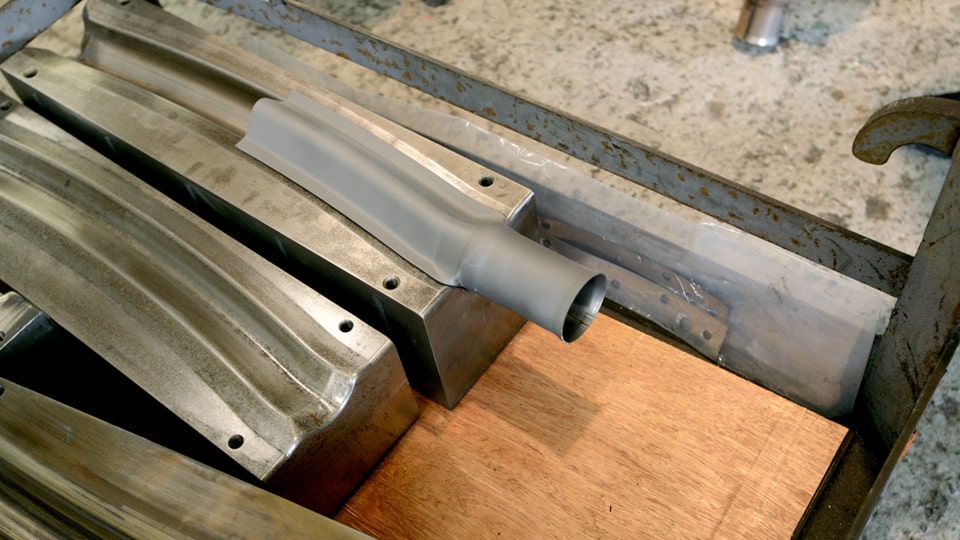
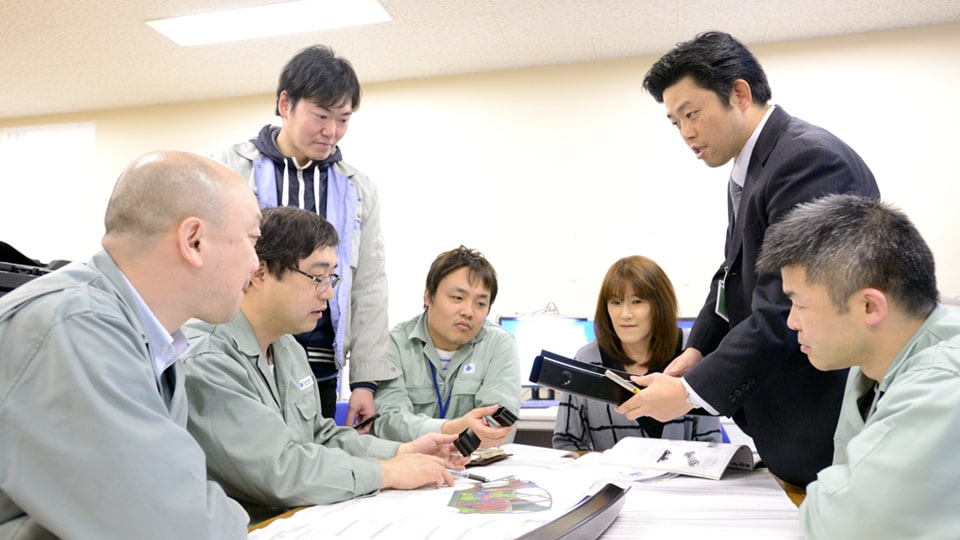
モノではなく、コトを提案することの大切さ
実験データが集まることで、ようやくコンピュータ・シミュレーションの条件が揃い出した。STAFを導入することで、他のプレス成形と比べ、車体フレームの耐荷重を3割以上高めることができることがわかった。同じ耐荷重であれば、板厚をより薄くし軽くすることができる。後からバリを取ったり、フランジをスポット溶接する必要もない。
「現在の試算では、車体フレームのプレス工程にかかる費用を2割以上少なくできるし、製造システムの設置スペースをよりコンパクトにすることができます。2016年度には評価機を開発し、自動車部品メーカーなどへの提案を進めていきます」と企画本部経営企画グループ・主任技師は胸を張る。
住友重機械工業がSTAFの開発を進めていることが2016年1月の「クルマの軽量化技術展」で初めて発表されると、ブースは人だかりになった。
もし、STAFが導入されれば、何十年と続いた車体フレームのプレス工程が様変わりする。ただ、課題がないわけではない。STAFの弱点は、他工法に比べ加工応用性が低いこと。例えば長手方向に湾曲したパイプなど複雑な形状については、開発の余地が残っており、汎用性を高めていくことが今後の課題だ。
新居浜の実験室に日本ではあまり設置されていない大型の高圧コンプレッサを設置するため、法律の解釈をめぐって県や経産省に日参し理解を求めた苦労も、ようやく報われる日が近づいている。企画本部経営企画グループ・主任技師はこのプロジェクトを通して多くのことを学んだ。
「自動車の軽量化に向けて世界中のメーカーやサプライヤーがしのぎを削っています。そのすべてが私たちのお客様になる可能性があります。そのためには、お客様に言われてから行動を起こすのでなく、それを見越して提案することが欠かせない。それを私はこのプロジェクトで学びました。もう一つは、“モノ”でなく“コト”を提案すること。お客様は単に安くて新しいプレス機が欲しいのではなくて、高品質なパーツを安定的に製造できるシステムを求められている。その期待にどれだけ応えられるかが重要なのです」
※記載内容は、すべて取材当時のものです。
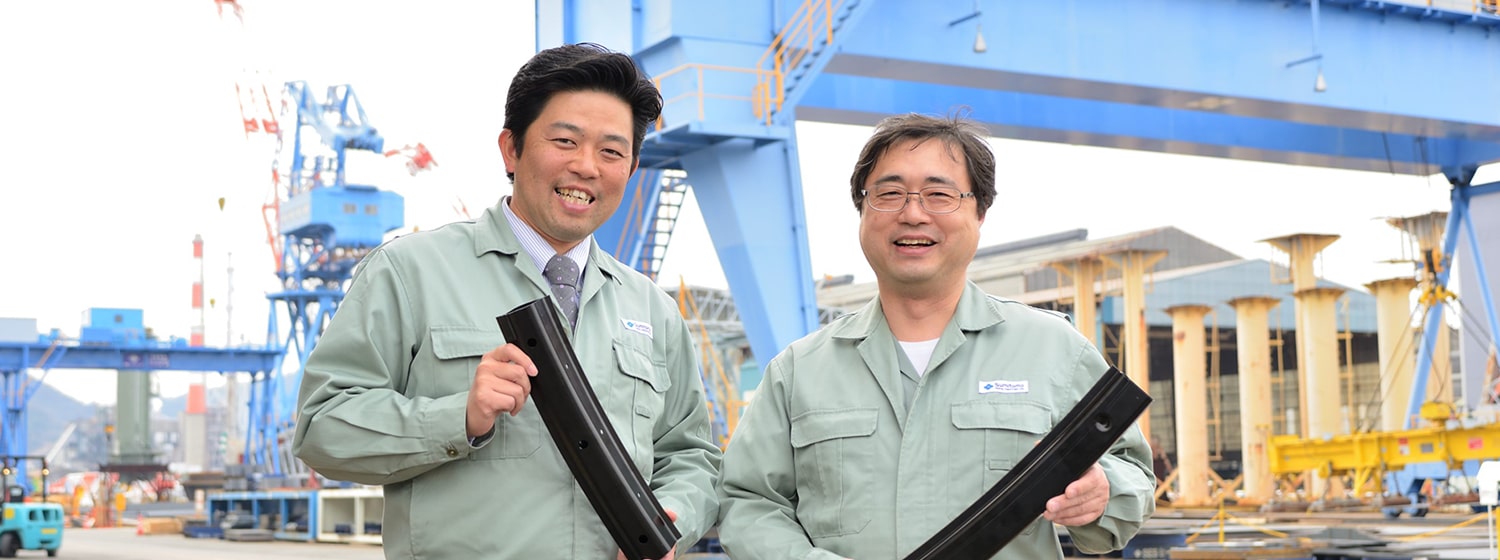