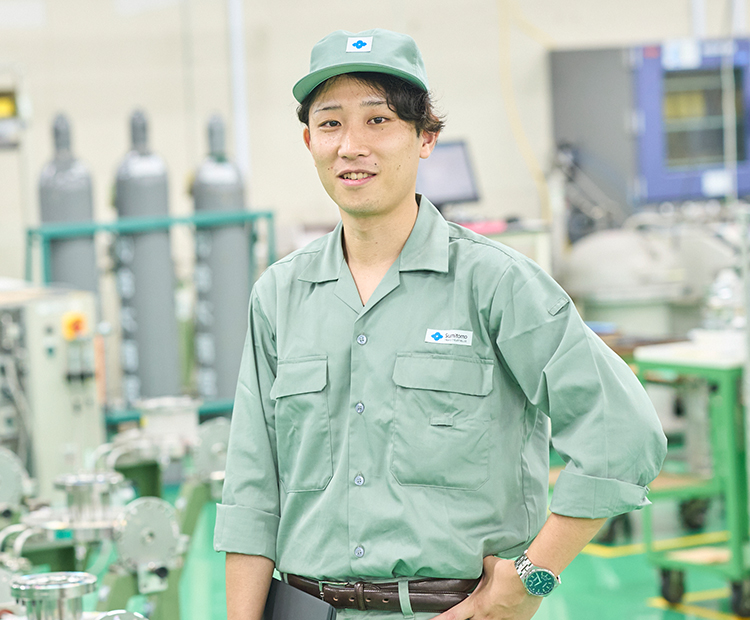
技術系|キャリア採用生産技術
半導体製造に欠かせない超高真空をつくる「クライオポンプ」。
少量多品種でありながら、
高効率・高品質なライン生産方式に挑む。
精密機器事業部 製造部 生産技術グループ
2022年入社
※所属、部門は取材当時のものです。
生産技術エンジニアとして
スキルアップできる環境を求めて出会った製品が
「クライオポンプ」だった。
クライオポンプとは、半導体製造装置に搭載される超高真空ポンプ。半導体の製造ラインにおけるキーコンポーネントのひとつです。私は、このクライオポンプの生産技術を担当しています。製造工程における改善や設備導入などに加えて、現在、新しい製造ラインの開発も任されています。
前職でも生産技術に携わっていました。扱っていた製品は小型精密機器。事業環境が変わって製造を縮小することになったのが転職を考えるきっかけでした。生産技術エンジニアとしてスキルアップできる環境があること。製品の需要が安定していて生産設備への投資に積極的なこと。この2つが転職の時に考えたポイントであり、当社への入社を決めた理由でもあります。
前職での製品は手のひらに乗るような小ささで、製造ラインは大量生産。一方、クライオポンプは腰の高さくらいのサイズがあり、製造も典型的な少量多品種生産です。まさに“技術のかたまり”のような機器で、その製造にも独自のノウハウがさまざまに活かされている。生産技術エンジニアとしてチャレンジしがいのある製品だと感じています。
少量多品種の組立をどこまで共通化できるか?
“セル”から“ライン”へ、生産ラインの刷新に取り組む。
これまでクライオポンプの製造は、1人の作業者が1台の製品を組み立てるという“セル生産方式”で行われきました。しかし、この方式では生産能力も限られ、効率化や品質管理などにも課題があります。そこで、数人の作業者がラインに沿って組み立てていく“ライン生産方式”に変革していこうというのが、現在私が取り組んでいる開発テーマなのです。
新しい生産方式を導入するためには、まず現状を的確に把握しなければなりません。そのため、製造の技術者にヒアリングするとともに、熟練作業スタッフの作業を撮影。長編映画1本分くらいある映像を何度も何度も見返しながら、工程の解析や無駄な作業の洗い出しなどを進めました。多品種の組立をどこまで共通化できるか? 重量のある製品をいかにライン上で搬送するか? 効率化を図るために随所にデジタル技術を導入しています。また、需要の変化に応じて生産量をフレキシブルに可変できる仕組みも取り入れました。現在(取材時点)は、モデルとなる仮の製造ラインを組み立てているステップ。開発を進めるにあたっては製造現場の技術者や作業スタッフたちと何度も打ち合わせを重ねました。効率や品質の追求ばかりでなく、作業スタッフたちが負荷なく快適に作業できる製造ラインの実現を目指しています。
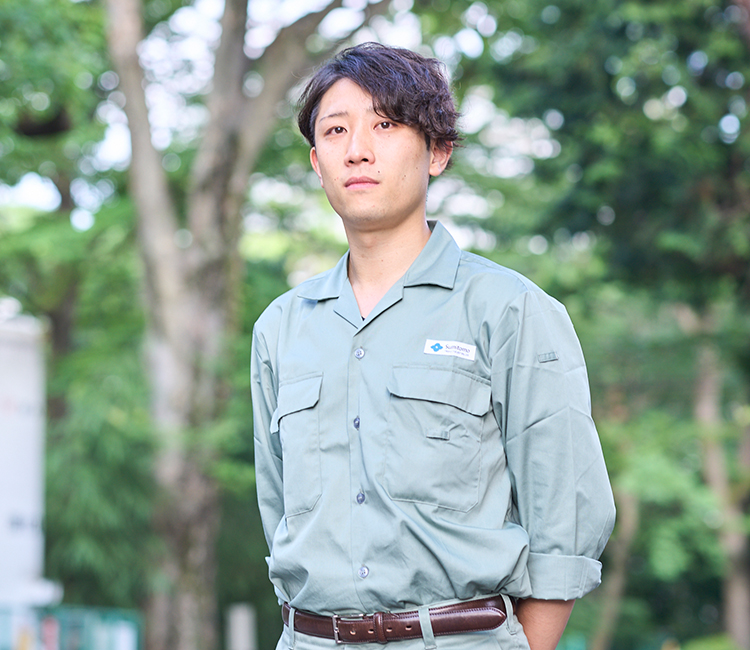
ものづくりの第一線で生産技術のスキルを磨き、
将来は、その経験を後輩たちに託していきたい。
ここ田無製造所では、事務棟と工場が同じ敷地内で、しかも歩いて数分という至近距離にあります。このように製造の現場が隣接していることも大きな特長でしょう。前職では、工場が海外など遠隔地にあり、不具合が発生した際などのやりとりがたいへんでした。工場との行き来だけでも時間がかかり、それが大きな負荷になっていたのです。その点、今の環境では、気になることがあればすぐに製造現場に飛んでいくことができます。効率的であるばかりなく、製造チームとも日頃から密にコミュニケーションをとることができ、生産技術エンジニアとして非常に恵まれた環境だと実感しています。
また、若手のうちから大きな仕事を任されること、そのチャレンジをまわりの先輩や上司が手厚くサポートしてくれることも、当社の事業では比較的新しい精密機器事業部が培ってきた風土だと感じています。
しばらくは第一線で生産技術エンジニアとしてのスキルを磨いていきたい。その先は、若手技術者の育成などマネジメント業務にも興味があります。自分が蓄積してきた経験やスキルを若手に託すとともに、後輩たちからも刺激を受けながらこれからもチャレンジを続けていきたいと思っています。
1 day Schedule
- 8:00
- 出社。チームの朝会の後、
メールチェック、スケジュール確認など
- 9:00
- 関係部署の技術者が集まり、
製造現場でミーティング
- 10:00
- チームでの週例会。進捗の確認、課題の共有など
- 11:00
- クライオポンプに関わるワーキンググループに参加
- 12:00
- 昼休み
- 13:00
- クライオポンプの工程設計、
チーム内でのレビューなど
- 17:00
- 退社