All-electric Injection Molding Machine for Lens


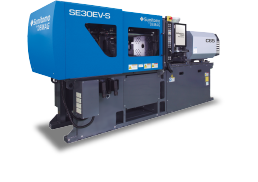
Platens keep high parallelism
Thermal Free Platens

The injection molding machine for lens adopts specially structured
Thermal Free Platens that minimize any irregular deformation due to heat,resulting in a platen that keep platen parallelism and straightness.
Thermal Free Platens that minimize any irregular deformation due to heat,resulting in a platen that keep platen parallelism and straightness.
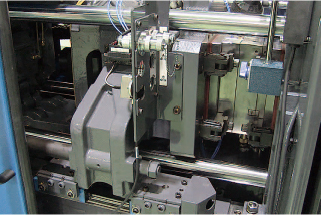
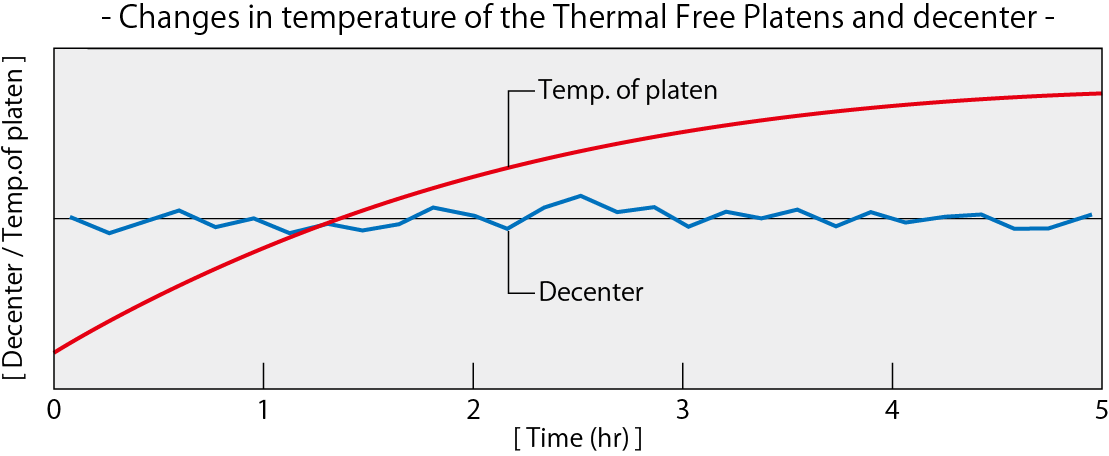
Conventional Platens
Heat flow model
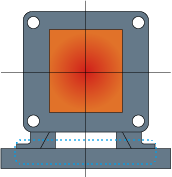
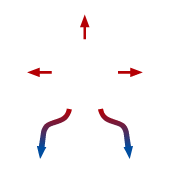
Temperatures differ above and below the platen
because heat propagated to the frame
Deformation accentuating model
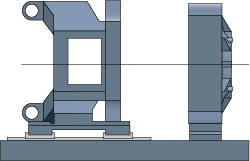
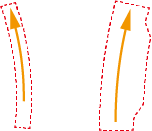
Deformation is uneven across the platen, so the platen does not stay flat.
Thermal Free Platens
Heat flow model
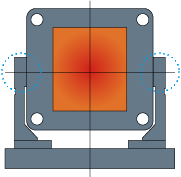
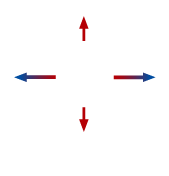
Heat propagates symmetrically upwards/downwards.
Temperature is the same above and below the platen.
Deformation accentuating model
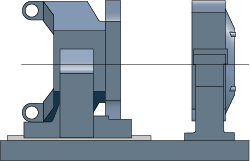
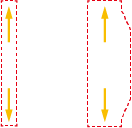
Upward/Downward deformation is even across the platen, so the platen stays flat.
Prevents tilting of fixed platen
High precision nozzle touch
The 2-axis support mechanism provides a load distribution centered on the nozzle.
Thus, it is possible to prevent the fixed platen from tilting during filling and holding pressure.
Thus, it is possible to prevent the fixed platen from tilting during filling and holding pressure.
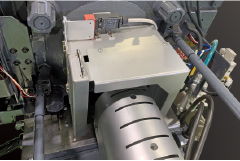
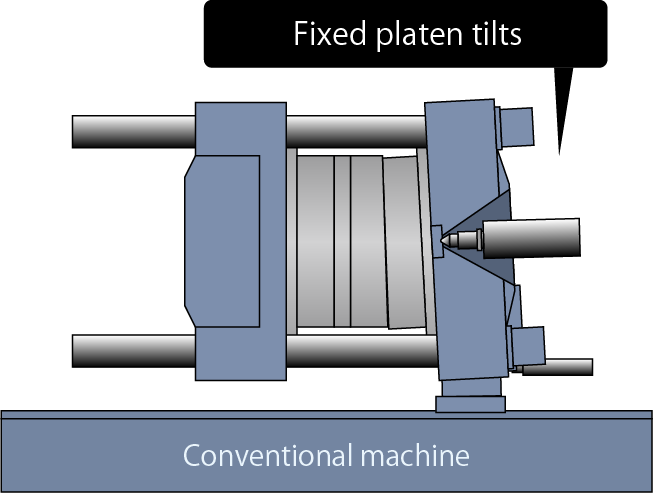
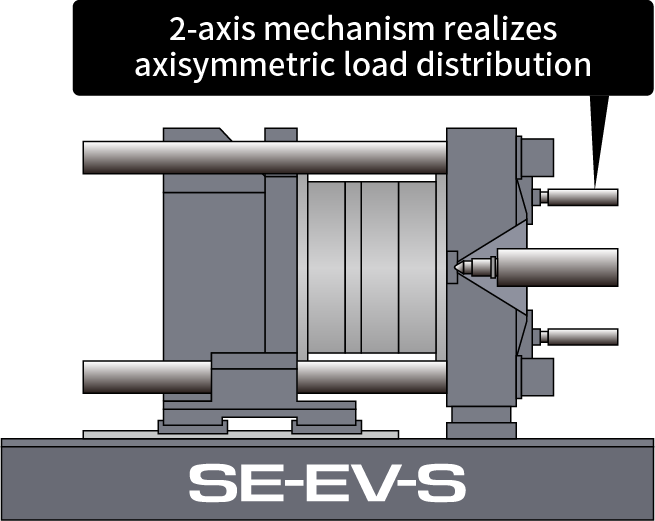
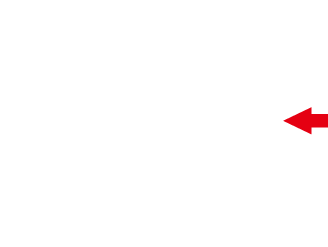
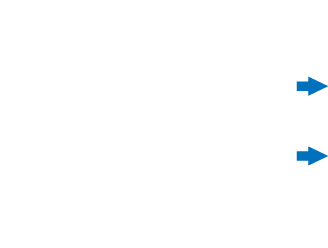
Prevents misalignment and galling
Nozzle touch force
feedback control
feedback control
Nozzle touch pressure-increasing/pressure-release can be controlled along
the molding process and set numerically.
It suppresses tilting of the fixed platen and deformation of the mold,
and prevents misalignment and pin galling.
It suppresses tilting of the fixed platen and deformation of the mold,
and prevents misalignment and pin galling.
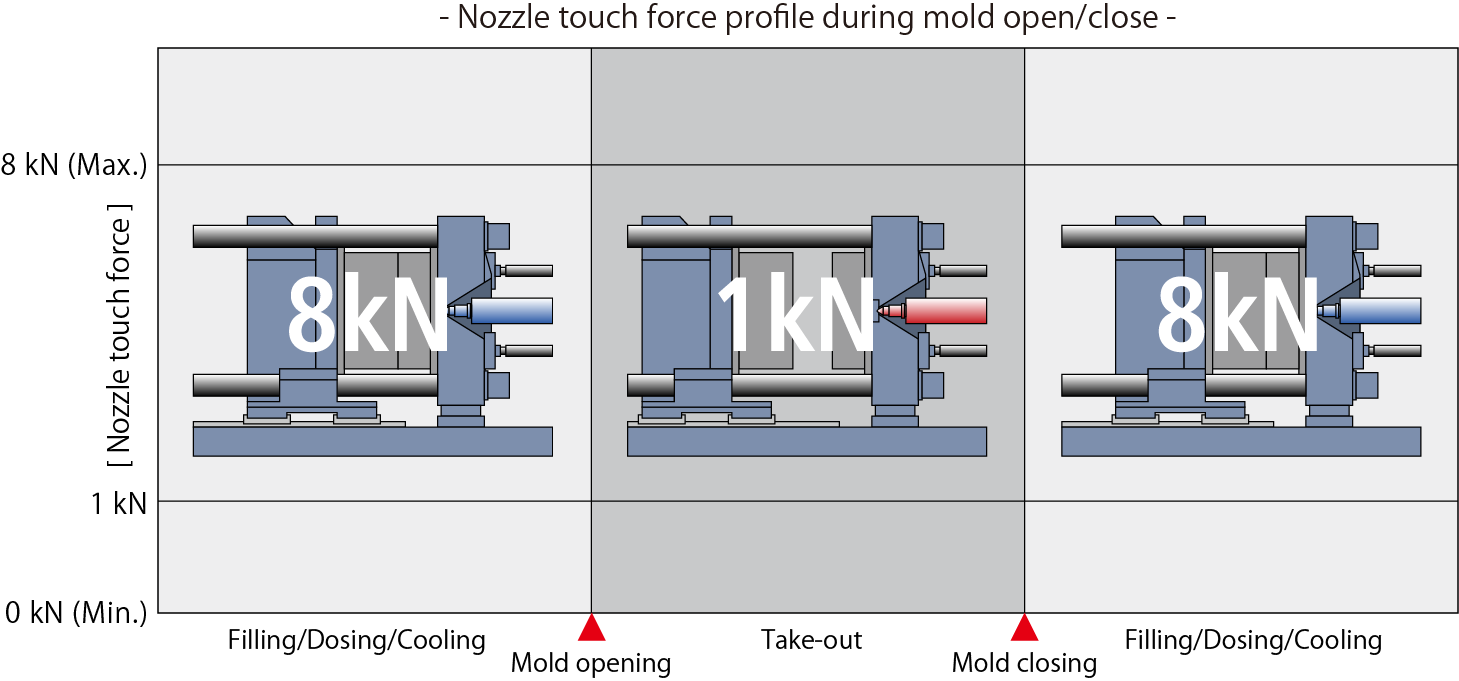
Optimal design for optical molding
Screw assembly for lens
Sumitomo offers two types of screw assemblies designed specifically for optical molding.
Type A keeps shearing force low to prevent resin from carburizing.
It works with all optical resins but is particularly effective in COC molding.
Type B is configured for extensive kneading (subflight) to prevent air bubbles and incomplete melting.The benefits are seen in molding COP and PC lenses.
Type A keeps shearing force low to prevent resin from carburizing.
It works with all optical resins but is particularly effective in COC molding.
Type B is configured for extensive kneading (subflight) to prevent air bubbles and incomplete melting.The benefits are seen in molding COP and PC lenses.
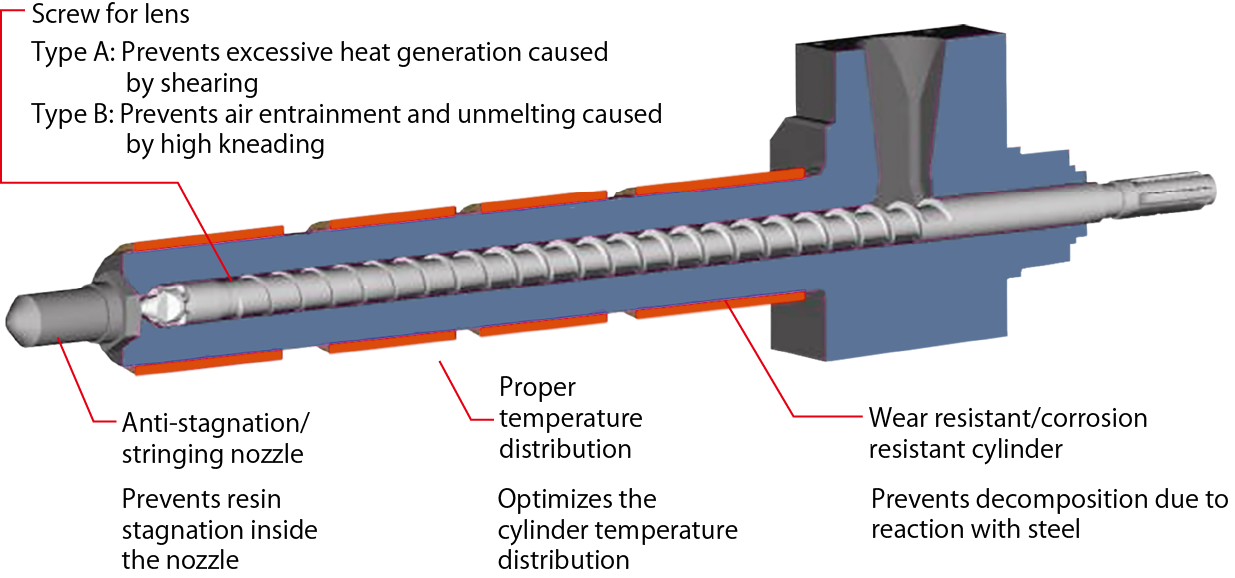
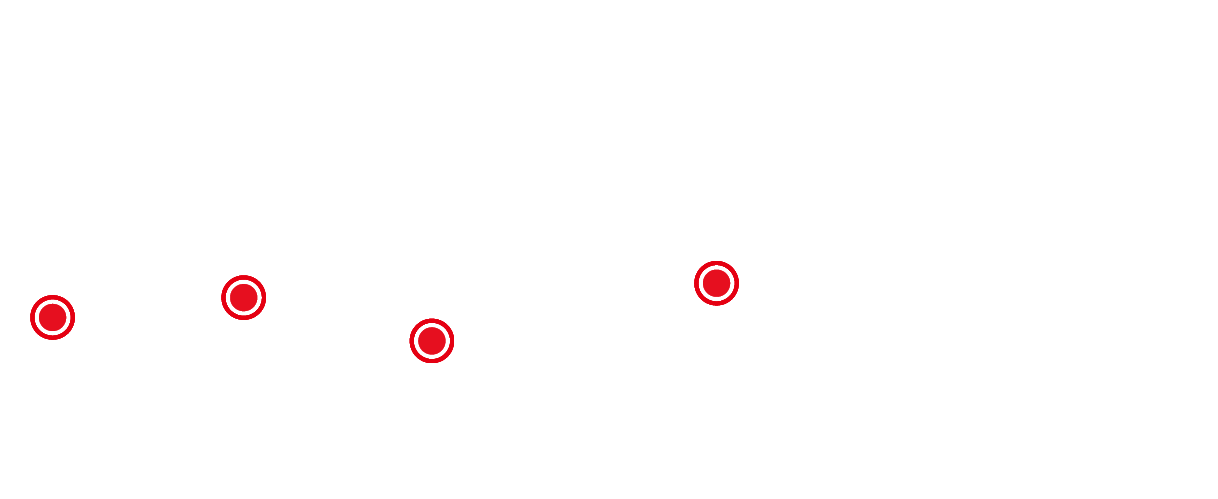
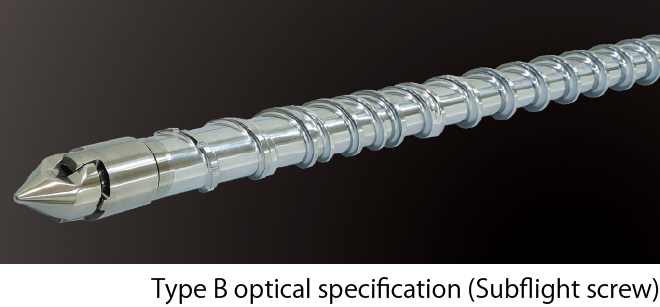
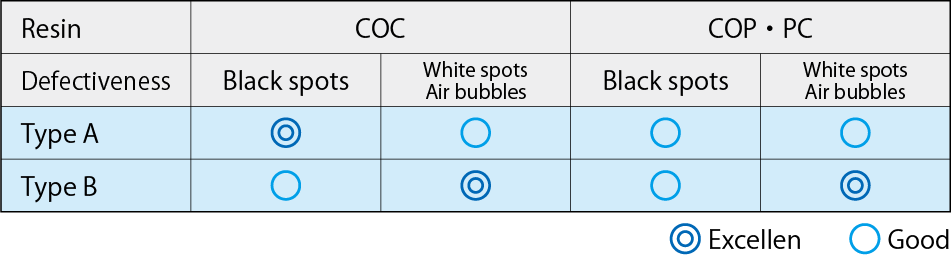
【 Comparison of defective rates】
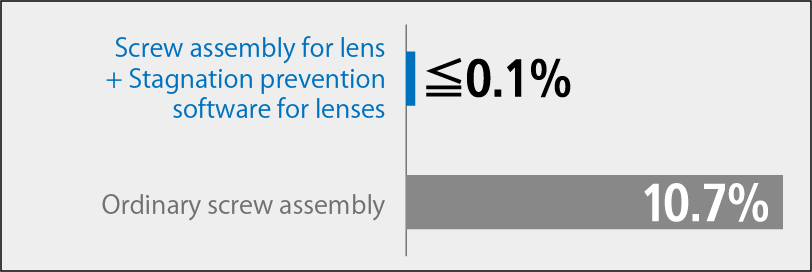
According to the conditions set by Sumitomo when using type A