


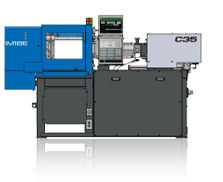
Smallest machine in 18 tf class
Reduces the footprint of
molding lines
The iM18E allows users to greatly shrink the amount of space occupied by equipment because it has the smallest footprint of any 18 tf class molding machine, comes with an injection unit that does not require turning and is designed so that peripheral units can be housed in the underbelly of the machine frame.
Because it recoups space, it allows users to build molding lines with more molding machines.
- Footprint comparison -
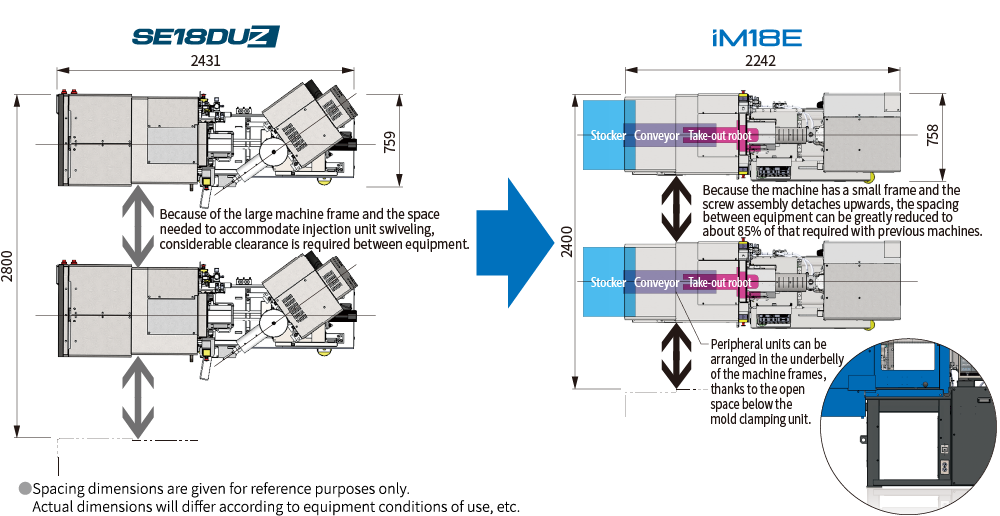
Half the power consumption of a hydraulic machine
Greatly reduces
running costs
A hybrid power drive and dramatic improvements in power-saving technology greatly reduce power consumption.
The energy reductions will help businesses realize sustainability goals.
- Power consumption comparison -
-
0.15kWh
-
0.31kWh
Achieves high-precision mold clamping in a compact manner
Hydraulic direct-pressure mold clamping unit
The hydraulic direct-pressure mold clamping unit improves gas purging, shortens setup time and makes the machine that much smaller.
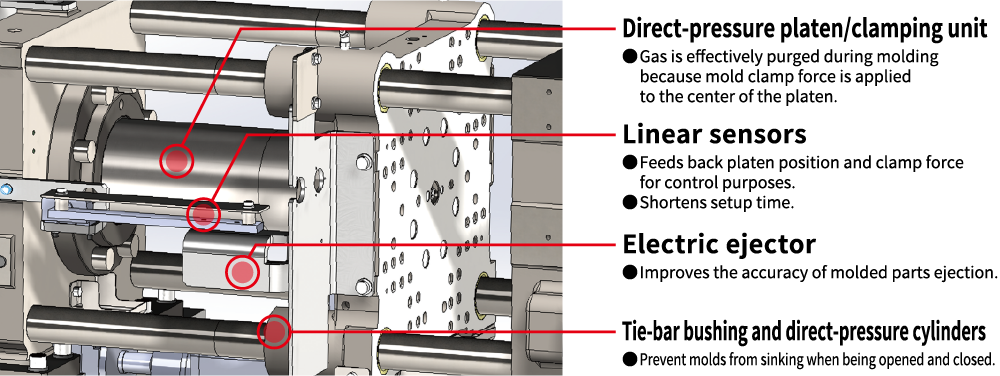
Stable high-precision in fast injection
Electric injection unit
The injection unit incorporates a low-inertia servomotor we developed ourselves.
It then uses a direct drive system and the ISC II (Intelligent Servo Controller II) to control the screw to a high degree of precision.
The improvements we made to both the hardware and control system have further enhanced precision stability and raised the top injection speed.
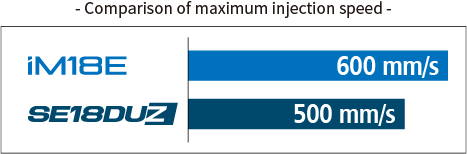
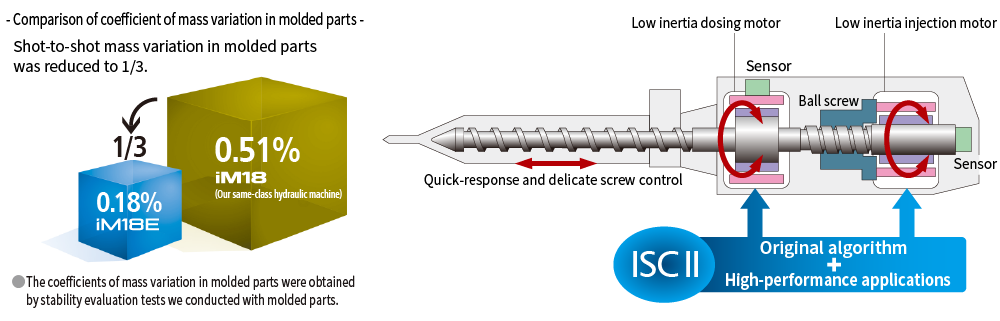
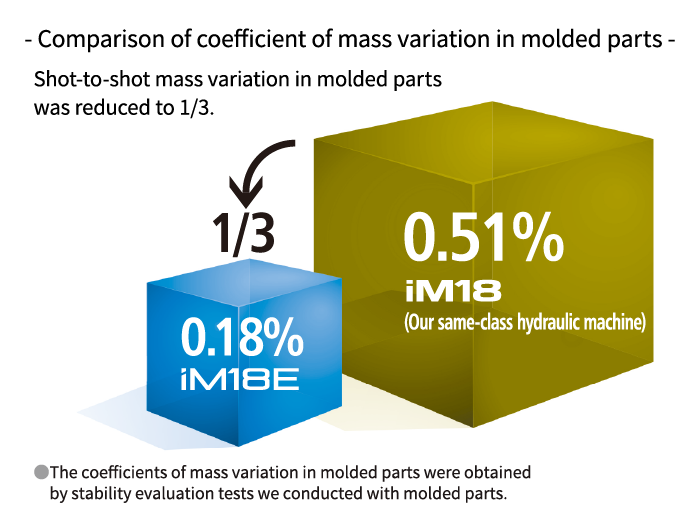
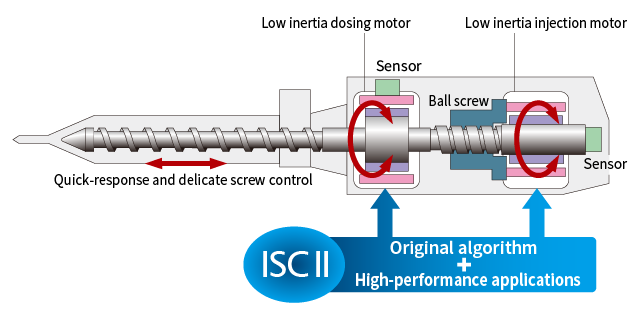
Higher accuracy at lower costs
Screw assembly
for connector
It stabilizes resin dosing and shot consistency, which greatly reduces the fluctuations in dosing time.
The dosing movement keeps to be stable even if crushed materials rate rises, which improves yield and reduces the material cost.
Connector spec B supports molding of environment-friendly resins such as halogen-free resin.
Optional
- Resin cost comparison -
- Connector
screw assembly -
- General
screw assembly
Cost-down and better productivity
FTC III nozzle
It prevents stringing and clogging by evenly distributing temperature using 2-zone temperature control.
In addition, its long protrusions reduce the resin consumption of the sprue and shorten the mold opening stroke, which shorten cycle time.
Moreover, heaters can be detached or attached simultaneously, which facilitates maintenance and shortens machine downtime.
Optional
- Maintenance cost comparison -
- FTC III nozzle
-
- FTC nozzle (Previous type)
Lineup