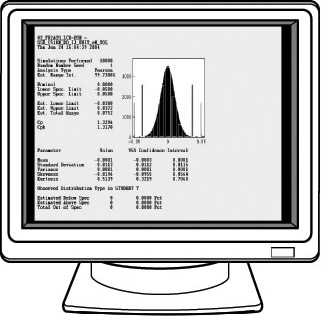
|
With the recent market requirement for higher accuracy,
the optimal setting of tolerance of working parts
in the development of new models of motored injection
molding machines has become much attention as a very
complicated and important issue in terms of determining
their mechanical specifications and manufacturing costs.
Meanwhile, with the conventional verification method
dependent on prototypes, there has been a tendency
that much time is required in designing and manufacturing,
retrogressive work is frequently inevitable if the
required specifications are not met, and immense development
lead time and cost are required. This paper discusses
a case in which a tool that enables a more efficient
design change through 3|D virtual part machining
and machine assembly in the initial development stage
was introduced and adopted in a developed model of a
motored injection molding machine (SE|D series) on a
trial basis, as a possible solution to these various problems. |
|