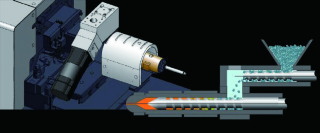 |
On the molding shop floor, molding is performed amid chronic plasticization-related problems, such as defective resin feeding, overheating, burning and gases. To cope with these, we recently developed a new theory plasticization system in cooperation with Spiral Logic Limited (SL), based on its new melting theory (Dynamic Uni-layer Melting Model). SL started developing plasticization systems designed to solve problems on the molding shop floor in 2002. By adopting a single-crystal sapphire in a visualization barrel, SL succeeded in measuring the temperature in the barrel. In addition, it concluded that the root cause of the molding problems was shearing heat generation by analyzing the results of measurement performed using a pressure sensor. The new theory plasticization system is a resin-melting system that eliminates shear elements; consisting of a volumetric feeding device (GS loader), a newly-designed screw (SL screw) and a new back-flow preventing mechanism (GS valve). The major features of the new theory plasticization system are: 1) stable molding, 2) reduced overheating, burning and gas impact, 3) a reduced impact from solid resin transportation, and 4) a shortened screw achieved through efficient resin melting.
|
|